Turbine air intake filters are crucial components in maintaining the performance and longevity of gas turbines by ensuring clean air supply, thus optimizing their operational efficiency and reliability. A suboptimal air intake filtration system can lead to increased wear, reduced efficiency, and potential system failures, highlighting the importance of selecting the right filters for your turbine systems.
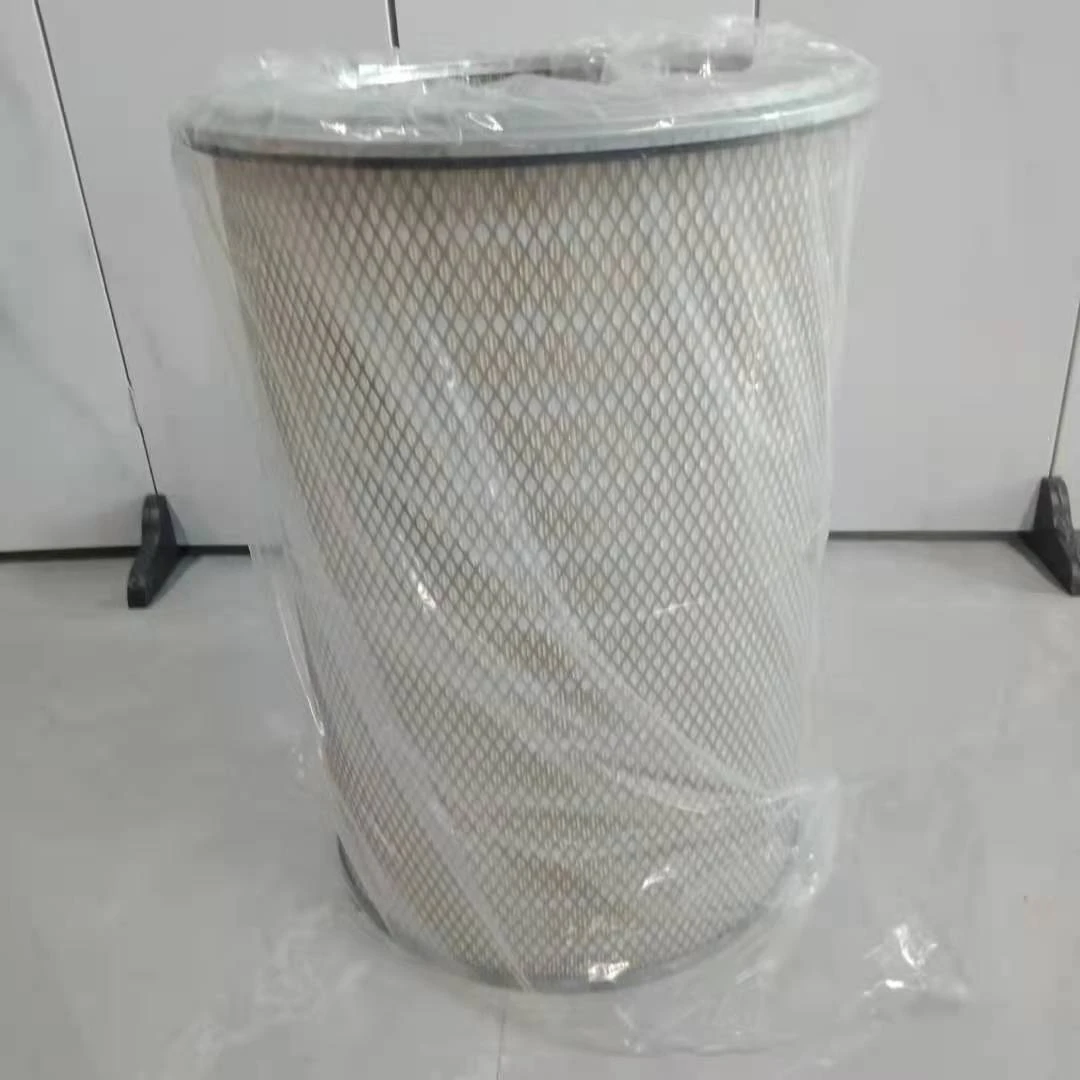
Experience has shown that having an effective air filtration system directly correlates with the operational stability and performance metrics of gas turbines. Through analysis of various case studies, turbine operators worldwide have observed significant improvements in maintenance cycles by prioritizing advanced air intake filter systems. These filters not only remove particulate matter but also protect against corrosive elements that may otherwise lead to premature turbine component degradation.
The technical expertise required in understanding turbine air intake filters is sophisticated, given that these filters must effectively handle diverse operational environments—from dusty deserts to humid coastal zones. When seeking high-quality filters, it's paramount to consider the filter’s efficiency, dust holding capacity, and pressure drop characteristics. An ideal filter provides a balance, offering high filtration efficiency without a substantial pressure drop which can otherwise reduce turbine output.
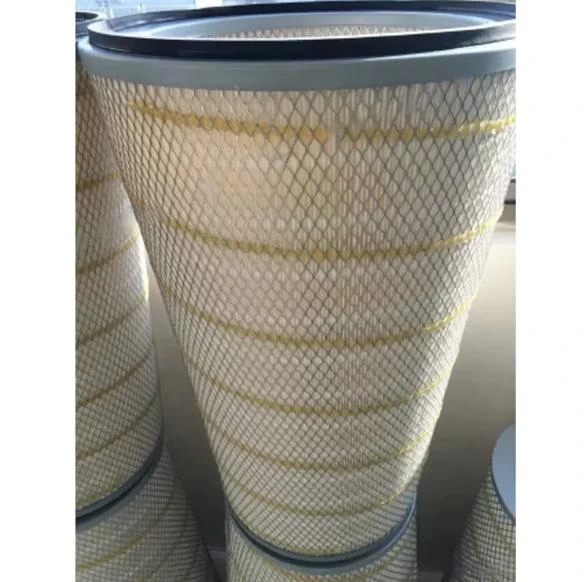
Authoritative sources within the industry, such as OEMs (Original Equipment Manufacturers) and leading engineering consultants, stress the necessity of utilizing filters designed specifically for the environmental conditions your turbine will face. A one-size-fits-all approach rarely produces optimal results. For example, filters with hydrophobic properties are invaluable in areas prone to high humidity, preventing moisture ingress that could compromise turbine performance.
Trustworthiness in the selection and maintenance of turbine air intake filters is achieved through rigorous testing and adherence to international standards, such as those prescribed by ISO 16890 or ASHRAE 52.2. Trustworthy manufacturers often subject their filters to extensive field testing, ensuring performance claims reflect reality. For end-users, partnering with suppliers who exhibit transparency in performance data and testing protocols significantly boosts trust and reduces the risk associated with substandard filtration solutions.
turbine air intake filters
Besides choosing the right filter, maintaining the air intake system is equally essential. Regular inspections and timely replacement of filters prevent the accumulation of particles that could otherwise lead to pressure drops and decreased efficiency. Implementing a proactive maintenance strategy, guided by the manufacturer's recommendations and adjusted for the specific operational environment, ensures that your filtration system remains effective throughout its lifecycle.
An often-overlooked feature of advanced air intake filters is their design adaptability. Recent innovations have introduced modular filter systems that allow for quick and easy replacements, minimizing turbine downtime. This modularity also permits the customization of the filtration setup according to seasonal variations and environmental changes, offering operators the flexibility to adapt to varying operational demands.
Furthermore, advances in filter material technology have led to the development of synthetic and hybrid materials, offering superior longevity compared to traditional cellulose filters. These advanced materials not only extend filter life but also enhance filtration capabilities, reducing the total cost of ownership while maintaining operational effectiveness.
In conclusion, turbine air intake filters are more than just a component; they are a linchpin in the operational success of gas turbines. Investing in high-quality, environment-specific filters, maintaining them rigorously, and choosing materials that adapt to operational challenges, reflects a commitment to excellence and reliability. By implementing these practices, operators not only ensure turbine efficiency and longevity but also significantly enhance their operation's overall performance and return on investment.