Sintered metal filter cartridges have carved a niche in industries where purity, reliability, and durability are paramount. These cartridges showcase unparalleled expertise when it comes to filtration, standing apart in today's competitive landscape by offering a unique blend of technological innovation and authoritative reliability.
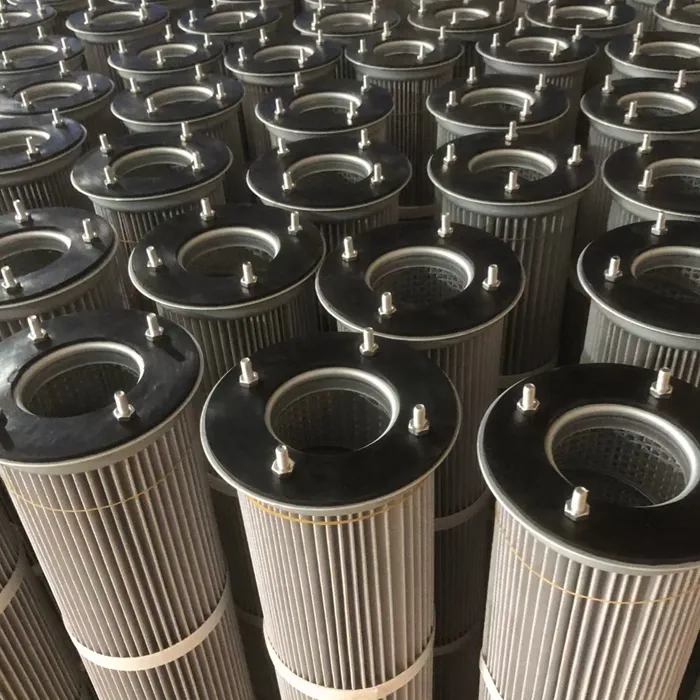
The journey of sintered metal filter cartridges began with a need for superior filtration solutions capable of withstanding harsh environments and rigorous applications. Unlike traditional filters, sintered metal filters are crafted using a process that fuses metal particles at high temperatures without melting them. This sintering process results in a porous structure that is precisely controlled, allowing for consistent and reliable filtration.
One of the standout features of sintered metal filter cartridges is their exceptional durability. Made from robust materials such as stainless steel, titanium, and other alloys, these filters can endure high pressures and temperatures that would typically compromise the integrity of other filter types. This robustness is indispensable in industries such as chemical processing, oil and gas, and pharmaceuticals, where the consequences of filter failure could be severe.

From an expert's perspective, the sintered metal filter cartridges offer a filtration spectrum ranging from a few microns to coarse levels. This versatility allows for customization based on specific industrial needs, making it possible to pivot between filtering out large debris and microscopic particles with remarkable precision. Furthermore, their corrosion-resistant properties ensure that these filters maintain their performance over extended periods, even when exposed to aggressive chemicals and abrasive media.
A practical testament to their trustworthiness lies in their minimal maintenance requirements.
Sintered metal filter cartridges can be cleaned and reused multiple times without a compromise in performance. Unlike single-use filters that require frequent replacements, these sintered cartridges prove to be cost-effective over time, providing substantial savings in operational expenses while also minimizing environmental waste—a critical consideration in today’s eco-conscious societal landscape.
sintered metal filter cartridge
In terms of real-world experience, industries have reported significant improvements in process efficiencies and product purity by integrating sintered metal filter cartridges into their systems. The seamless compatibility with existing setups and their long operational life have translated into less downtime and enhanced throughput. The straightforward cleaning process, often involving backwashing or chemical cleaning techniques, further underscores their utility, ensuring production lines remain in optimal condition with minimal interruption.
Authoritative institutions and industry standards acknowledge the superiority of sintered metal filters. Compliance with stringent regulations such as ISO requirements highlights their fit for purpose in sensitive applications. Engineers and process designers often advocate for their implementation, not merely as a recommendation but as a strategic enhancement to operational reliability and product quality.
The trust placed in sintered metal filter cartridges extends to their role in research and development facilities. Their predictable performance provides scientists with the confidence needed in experimental setups, ensuring that only the variables intended for study are present, without external contamination.
In conclusion, the sintered metal filter cartridge stands as a paragon of filtration excellence, combining expertise-driven design with authoritative performance reliability. For businesses seeking to enhance their filtration processes, the adoption of these cartridges is not just a choice; it is an investment into the very foundation of product integrity and operational efficiency. As industries continue to innovate and demand evolves, sintered metal filter cartridges remain at the forefront, ready to meet and exceed the challenges of tomorrow’s filtration needs.