In the rapidly evolving landscape of industrial technology, the silo filter cartridge stands out as a critical component. Its primary role revolves around purifying air by trapping dust particles and preventing them from contaminating stored materials. This ensures both product integrity and environmental compliance, essential imperatives for industries ranging from agriculture to manufacturing.

Silo filter cartridges find their foundation in the principles of efficient air filtration. They’re crafted with materials designed to withstand harsh industrial environments while providing long-lasting performance. Robust construction is of utmost importance; hence, manufacturers typically use high-grade cellulose, polyester felt, or advanced composite materials. These materials support the durability needed to endure constant exposure to dust-laden air while maintaining optimal filtration efficiency.
From an expertise standpoint, understanding the inner mechanics of a silo filter cartridge can enhance performance and longevity. Cartridges are equipped with pleated designs, increasing the surface area for filtration without enlarging the filter itself. This allows for higher dust holding capacity, reduced pressure drop, and efficient filtration, even under high flow conditions. This expertise helps industries reduce operational costs, as the need for frequent replacements diminishes.
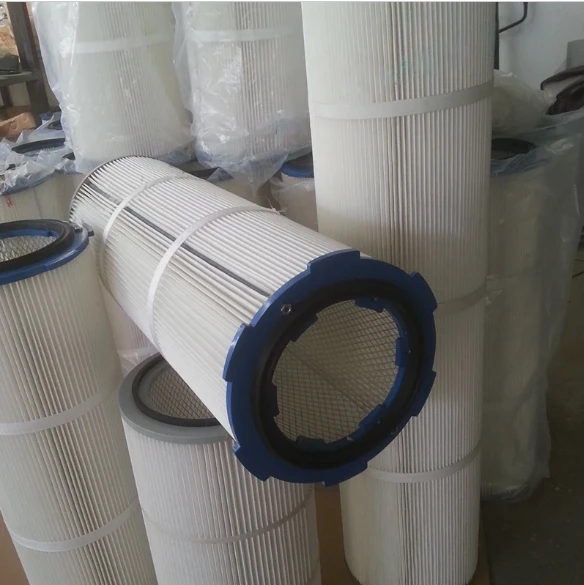
The authority on silo filter cartridges begins with understanding international standards such as the ASHRAE and ISO filtration standards. These guidelines ensure a minimum efficiency reporting value (MERV) that guarantees the cartridge’s performance in capturing specific particle sizes. A reputable manufacturer will adhere to these standards and provide certifications attesting to the performance capabilities of their cartridges. Such adherence is a mark of quality assurance and reflects superb authoritativeness, reassuring industries of the product’s reliability.
silo filter cartridge
Practical experience also underscores the essential maintenance and operational tips that ensure the long-term functionality of silo filter cartridges. Regular inspections to check for damages or clogging help in identifying potential leakage risks early on. Employing techniques such as pulse jet cleaning, involving bursts of compressed air, ensures the filter media remains clean and efficient over extended periods. Implementing such maintenance protocols requires minimal downtime and leverages advanced remote monitoring systems to relay real-time data on the filter’s performance.
Selecting the right silo filter cartridge hinges on a careful assessment of the specific industrial application. Parameters such as temperature resistance, chemical compatibility, and flow rate requirements must be matched with the cartridge’s technical specifications. Customization options also provide considerable flexibility, allowing industries to modify filtration capacities in alignment with unique operational demands. This tailored approach amplifies the trustworthiness of the cartridge’s performance, bolstering confidence in preserving the quality of stored goods.
Trust is further built through testimonials and case studies shared by industries benefiting from upgraded filtration systems. Narratives of enhanced productivity, cost savings from reduced maintenance, and compliance with environmental regulations paint a vivid picture of the silo filter cartridge’s impact. Sharing these experiences within an industry network elevates trust levels, encouraging potential users to invest in such filtration systems.
In conclusion, the silo filter cartridge is far more than a simple filter. It embodies a critical intersection of engineering expertise and practical application, ensuring industries maintain clean operations. By adhering to high standards of quality and amplifying operational trust, these cartridges serve as indispensable tools in safeguarding both industrial productivity and environmental responsibility. They symbolize an investment in superior solutions that align with both present demands and future filtration challenges.