The metal filter element, an indispensable component in various filtration systems, stands out due to its robust features and versatile applications. Unlike conventional filters, the metal filter element is celebrated for its durability, resistance to extreme conditions, and ability to provide long-lasting service. This level of resilience makes it an essential resource across various industries, from automotive to food production, highlighting its broad utility and importance in ensuring operational efficiency and safety.
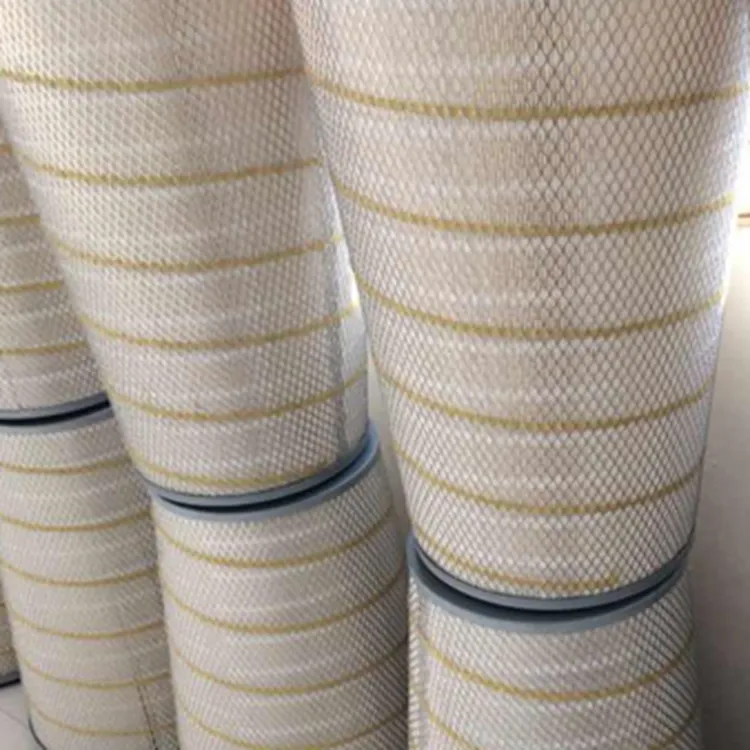
One of the primary advantages of the metal filter element is its structural integrity. Composed of high-quality metals such as stainless steel, bronze, or nickel, these filters can withstand significant thermal and pressure fluctuations, which is essential in industrial environments. This structural robustness not only extends the life of the filter but also reduces the frequency of maintenance, leading to cost savings and reduced downtime – a crucial factor for any industrial operation aiming for efficiency and profitability.
In industries such as oil and gas, where equipment operates under high pressure and temperature, the reliability of filtration systems is paramount. Metal filter elements effortlessly handle the harsh conditions found in such environments, filtering out impurities that could otherwise lead to equipment failure or contamination of the product. Their high dirt-holding capacity and resistance to corrosion make them ideal for tasks that demand impeccable filtration performance and reliability.

Moreover, metal filter elements are not just about durability and performance.
They are also eco-friendly. With global emphasis shifting towards sustainable solutions, the recyclable nature of metal filters presents an environmentally responsible alternative. Unlike disposable filters that contribute to waste, metal filter elements can be cleaned, re-used, and eventually recycled, aligning with modern sustainability goals and practices.
metal filter element
For businesses seeking customization, metal filter elements offer unparalleled versatility. They can be tailored to meet specific requirements concerning pore size, shape, and material composition, addressing unique filtration needs. This customization capability ensures that users can achieve optimal filtration effectiveness, crucial for maintaining product quality and meeting regulatory standards, particularly in stringent industries like pharmaceuticals and food processing.
Additionally, the advancement in manufacturing technology has enhanced the precision of metal filter elements. Techniques such as sintering and mesh weaving enable the production of intricate filter designs that ensure even the tiniest particles are filtered out, a necessary feature for processes requiring the highest purity levels. This precision contributes to the overall reliability and performance of the filtration system, ensuring that users can trust these components to perform consistently under varying conditions.
The expertise behind metal filter element manufacturing is grounded in a deep understanding of material sciences and engineering. Manufacturers invest heavily in R&D to continuously improve the efficiency and capability of their products, ensuring they meet the ever-growing demands of modern industrial applications. This continuous innovation is a testament to the expertise and authoritative knowledge that manufacturers possess, providing confidence to users that they are investing in tried-and-tested technology.
In summary, the metal filter element is more than just a component in a filtration system; it is a testament to advanced engineering and material science. Its robust construction, eco-friendly profile, customization options, and precision performance make it an unmatched solution in various industrial applications. The authority and trust it commands in the industrial sector are well-earned, being a key player in ensuring operational safety and efficiency. As industries evolve, the role of the metal filter element will undoubtedly expand, bridging the gap between traditional filtration needs and modern environmental and performance standards.