In the complex world of industrial machinery and power generation, gas turbines stand as vital components due to their efficiency and capability to handle high loads. Central to their operation is a component often overlooked yet crucial for performance—air filters. Delving into the nuances of gas turbine air filters reveals the importance of experience, expertise, authoritativeness, and trustworthiness in selecting and maintaining these components.
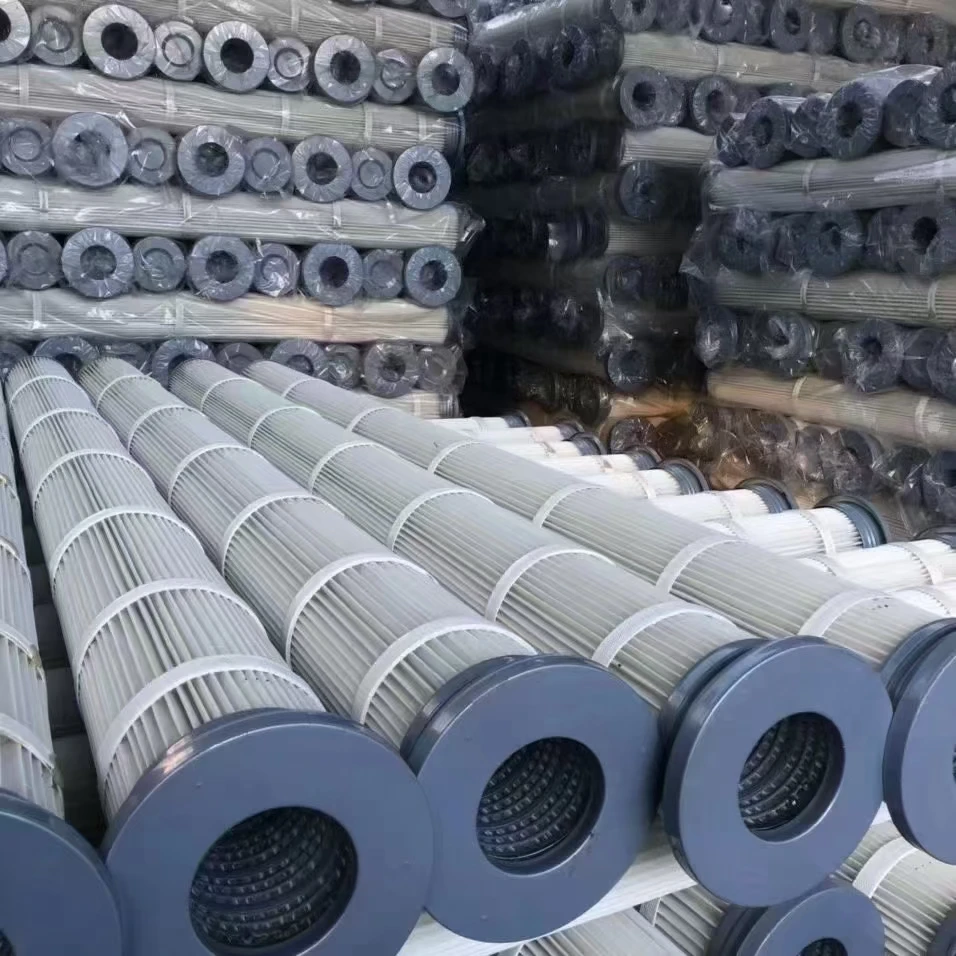
Gas turbine air filters serve as the lungs of the turbine, tasked with the critical role of cleansing intake air. This air, when mixed with fuel, produces the combustion necessary to drive the turbine blades. Clean air ensures optimal combustion, reducing maintenance costs and enhancing the lifespan of the turbine. Thus,
the performance of a turbine is intimately connected to the effectiveness of its air filter.
The engineering intricacies behind gas turbine air filters showcase expertise in action. These filters are designed to trap fine dust, pollen, soot, and even harmful air pollutants that can potentially scale or corrode the turbine components. High-quality filters possess a multi-layered design, often incorporating both coarse and fine filtration technologies. This layered approach not only ensures the capture of larger debris but also stops microscopic particles that can evade single-layer systems.
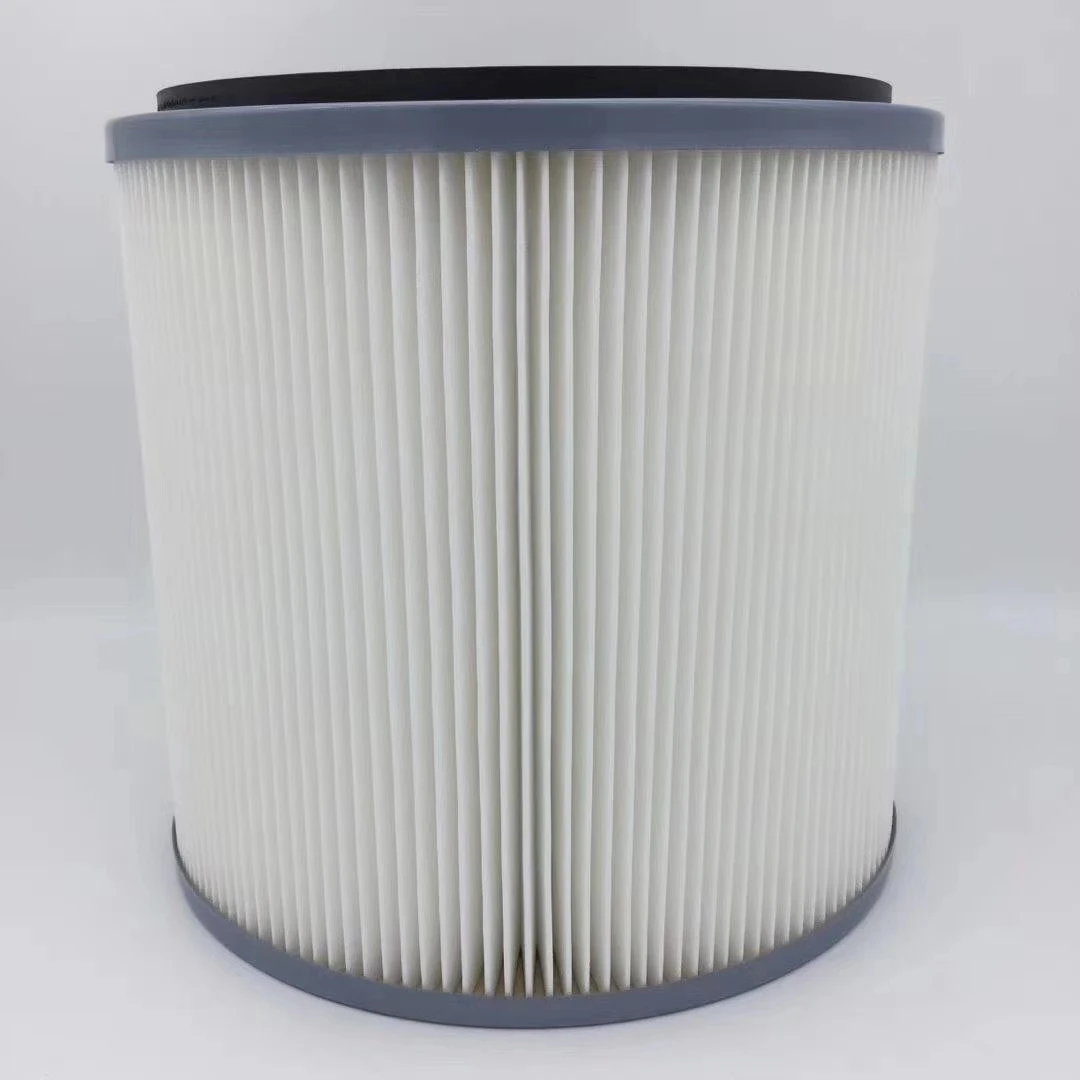
Expertise also manifests in the material selection for these filters. Advanced filters use media like synthetic fibers or micro-glass layered structures to enhance durability and capture efficiency. The synthetic materials provide resilience against moisture and environmental degradation, a common challenge faced by air filters, thus assuring consistent performance even in harsh climates.
Authoritativeness in the realm of gas turbine air filters is demonstrated by adherence to industry standards and certifications. Filters are subject to rigorous testing procedures, conforming to standards such as the ISO 16890 or ASHRAE 52.2. These protocols dictate the allowable limits of particle penetration, filtration efficiency, and integrity under stress conditions. Purchasing filters from certified manufacturers assures users of product reliability and performance backed by empirical testing and validation.
gas turbine air filter
Trustworthiness in a gas turbine air filter supplier or manufacturer is built over time through proven performance records and customer satisfaction. Real-world operational data, showcasing filter performance in diverse environmental conditions, builds confidence among consumers. Furthermore, the availability of personalized support services, such as expert consultations and maintenance assistance, enhances trust in the product and the brand.
Field experience illustrates that the meticulous selection and upkeep of gas turbine air filters can lead to measurable efficiency gains. For instance, optimizing filter selection based on the specific environmental conditions of turbine operation can significantly enhance air quality management within the system. In coastal or industrial environments, where salt or particulate pollution is prevalent, targeted filter solutions lead to notable reductions in turbine wear and maintenance frequency.
Transitioning to routine maintenance, real-world experience underscores the importance of regular inspection and timely replacement of air filters. A proactive replacement schedule, informed by pressure differential readings and contamination levels, prevents the detrimental effects of clogged filters which can cripple turbine efficacy and result in unwarranted downtimes.
Moreover, adopting data-driven methodologies enhances the predictability of maintenance needs and operational cost forecasting. Utilizing advanced monitoring systems that track filter pressure drops and environmental conditions in real-time empowers operators with insights for proactive decision-making.
In summary, understanding the pivotal role of gas turbine air filters requires a synthesis of experience, expertise, authoritativeness, and trustworthiness. The careful selection, usage, and management of these components stand as testaments to an organization’s commitment to operational excellence and sustainability. Investments made towards high-quality filtration systems are, unequivocally, investments towards sustained turbine performance and longevity—critical factors in the highly demanding world of power generation and industrial machinery.