The role of the gas turbine air filter in ensuring optimal performance and efficiency of gas turbines cannot be overstated. Gas turbines, widely used across various industries such as power generation, oil and gas, and aviation, rely heavily on the purity of the intake air to function effectively. Contaminants like dust, pollen, smoke, and other particulates can severely diminish the efficiency and lifespan of these turbines. The air filter, therefore, stands as a critical component within the gas turbine system, ensuring clean air intake and safeguarding the machinery from wear and tear.
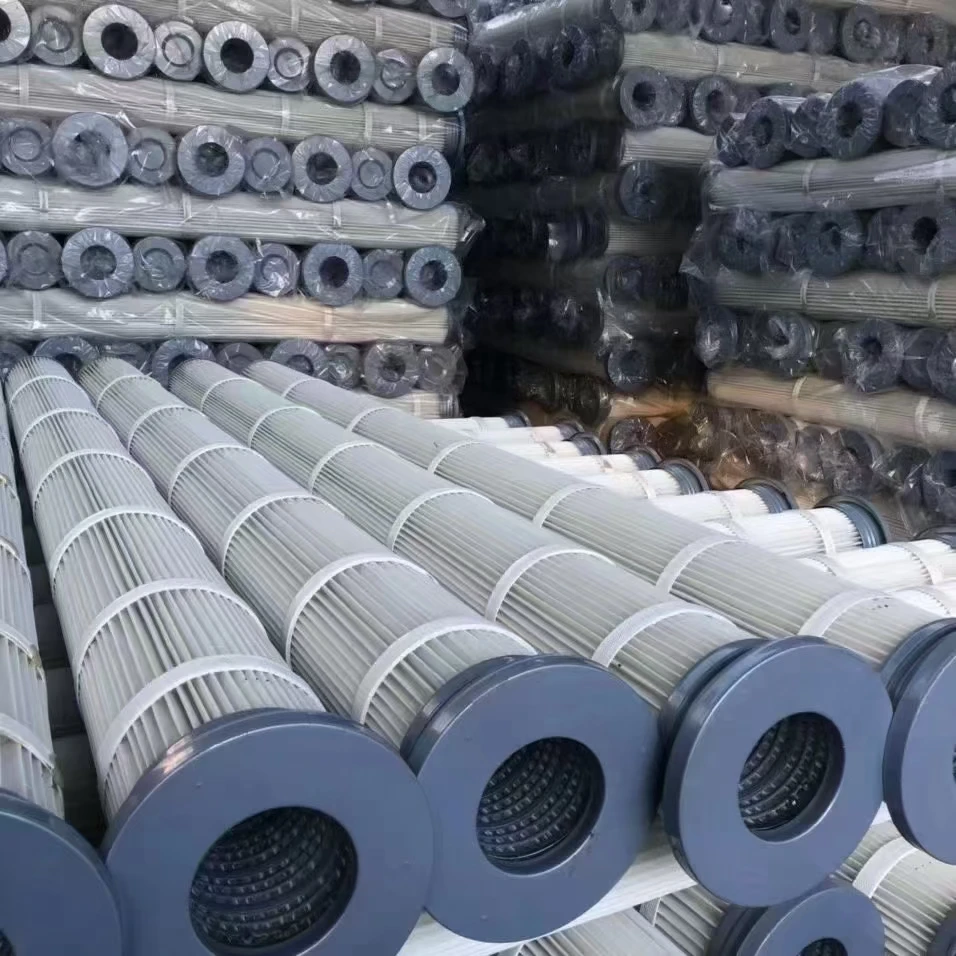
At the heart of the gas turbine air filtration technology is its meticulous design, which balances pressure drop, filtration efficiency, and dust holding capacity. A high-quality gas turbine air filter typically integrates multiple layers, combining synthetic and natural fibers that ensure maximum filtration without compromising airflow. This layered approach not only enhances the filter’s ability to capture microscopic particles but also extends its operational lifecycle.
Experience from industry experts highlights the importance of tailoring gas turbine air filters to specific environmental conditions, such as coastal, desert, or industrial areas. In coastal regions, high humidity combined with salt can lead to corrosion, necessitating filters that can handle moisture and saline particles. Desert areas, on the other hand, pose challenges due to fine dust and sand, requiring robust dust holding capacities. Meanwhile, industrial areas may expose turbines to chemical pollutants, demanding specialized filters that can neutralize or capture harmful particles.
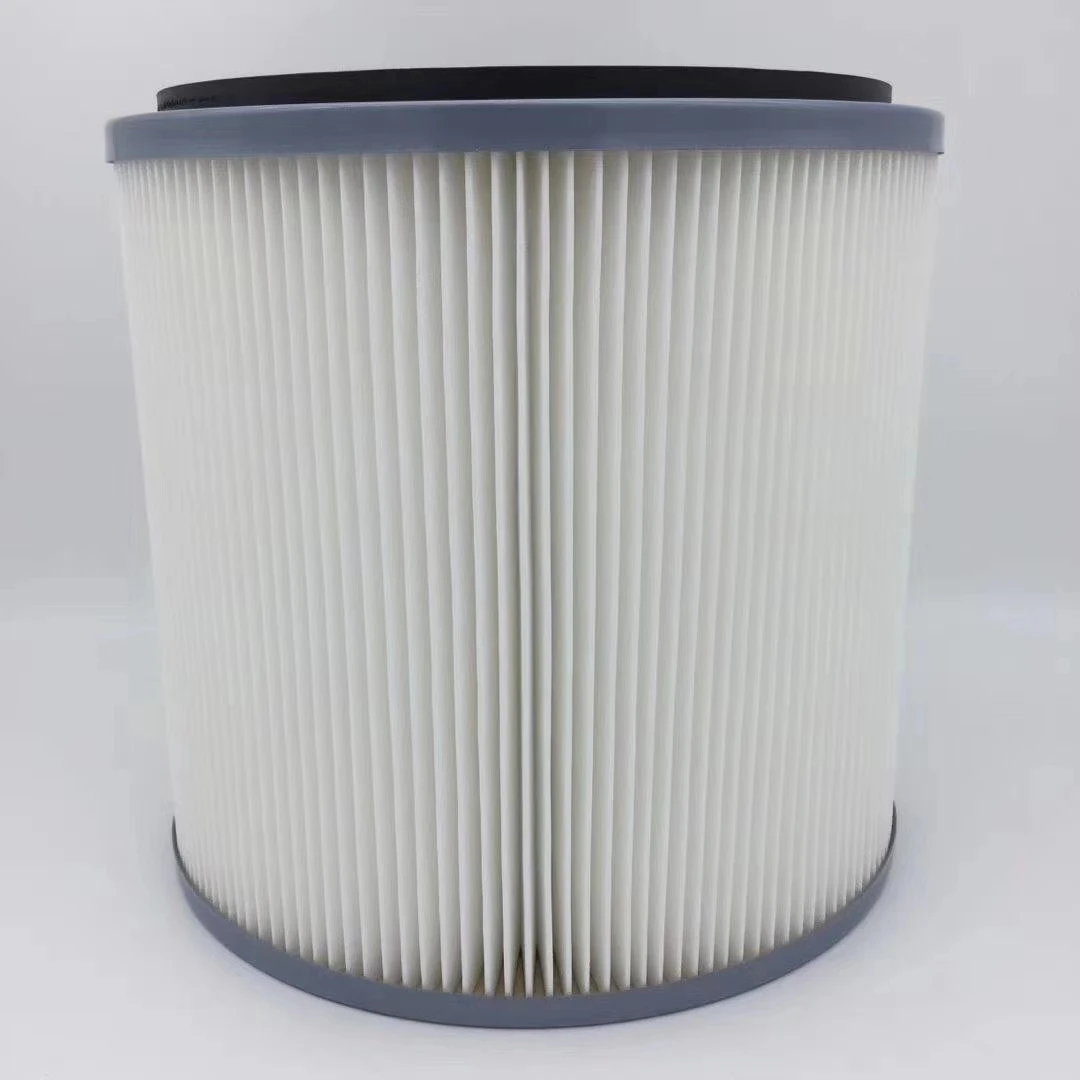
Manufacturers leverage cutting-edge technology, including nanofiber materials, to improve the filtration surface area and enhance particulate capture rates. This advancement in material science translates into filters that not only meet but often exceed industry standards for air purity. The use of advanced nanofiber technology is a testament to the ongoing evolution in filter design, ensuring gas turbines operate at peak efficiency regardless of environmental challenges.
Authoritative studies and field research consistently underscore the correlation between efficient air filtration and reduced maintenance costs for gas turbines. By preventing debris and particulate accumulation, air filters decrease the frequency of turbine downtimes and the need for expensive repairs or cleaning procedures. Organizations like ASME (American Society of Mechanical Engineers) and ISO (International Organization for Standardization) provide stringent guidelines and standards that help manufacturers develop air filters that are both reliable and effective.
gas turbine air filter
Moreover, the trustworthiness of a gas turbine air filter is often measured by its compliance with these international standards. Certifications from credible institutions signal that the filters have undergone rigorous testing to assure their quality and performance under various operating conditions. Companies investing in high-standard filters benefit from a protective layer of assurance, knowing their filtration systems meet global best practices.
Real-world installation case studies reveal dramatic improvements in turbine efficiency and durability when operators choose premium filtration solutions. For instance, a power plant in the arid regions of the Middle East experienced a remarkable reduction in turbine blade erosion after deploying specialized high-dust holding capacity air filters. Similarly, an offshore wind farm reported a significant decrease in salt-induced corrosion after switching to filters designed for high-moisture environments, demonstrating the critical role of context-specific filter solutions.
The overarching consensus among engineers and maintenance experts is clear the integrity of a gas turbine significantly depends on the efficiency and reliability of its air filtration system. As the demand for gas turbines increases in various industries, the need for advanced air filters that enhance turbine performance and longevity becomes more pronounced. Those involved in gas turbine operations are encouraged to partner with reputable filter manufacturers who invest in research and innovation, ensuring their products meet the evolving needs of technological and environmental changes.
In conclusion, the gas turbine air filter is an invaluable asset in the functionality and protection of gas turbines. Its intricate design and adaptability to different environmental conditions underscore its significance in maintaining turbine efficiency and reducing operational costs. As technological advances continue to push the boundaries of what air filters can achieve, the focus remains steadfast on quality, compliance, and reliability, ensuring the prolonged performance of gas turbines worldwide.