Selecting the right air filter for a gas turbine isn’t merely a maintenance task—it's a strategic decision that impacts turbine efficiency, longevity, and environmental compliance. One profound aspect to consider is the filter’s ability to maintain optimal airflow while effectively capturing particles.
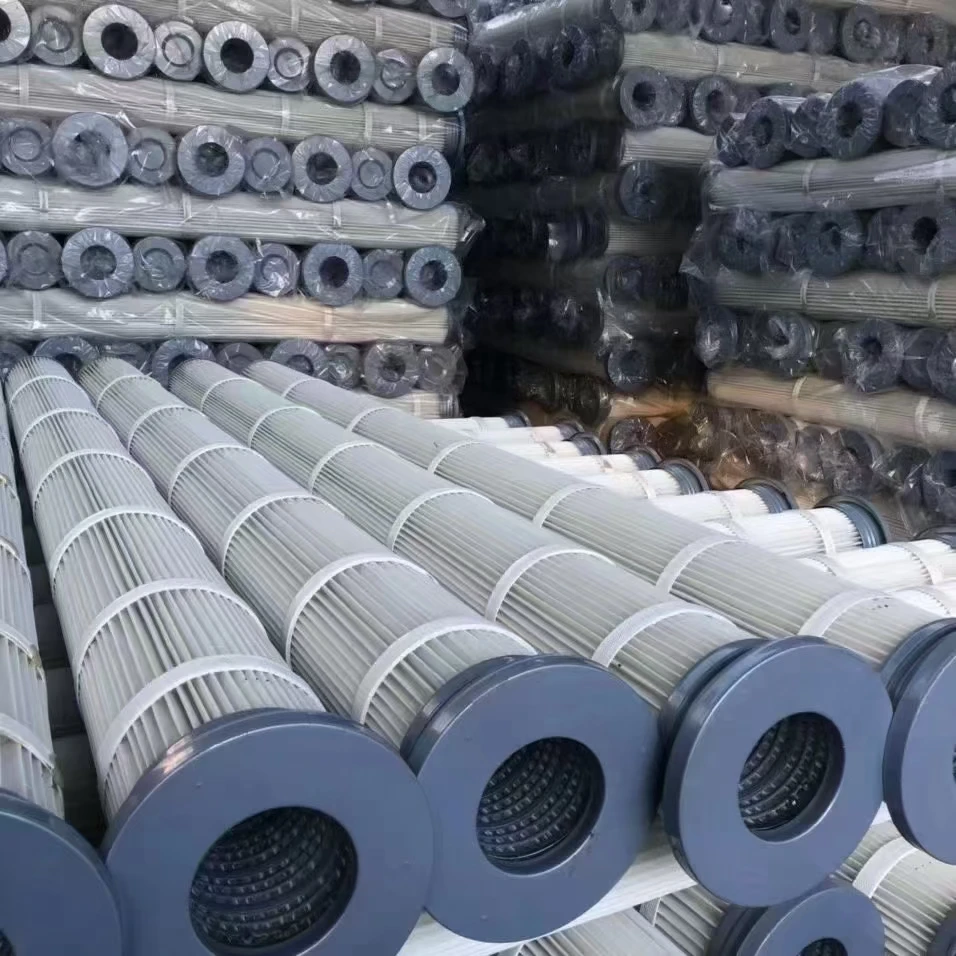
Real-world experience has shown that high-performance filtration systems can reduce particulate intrusion by over 50%, significantly lowering maintenance costs and downtime. This improvement is crucial in dusty and industrial environments, where foreign particles can rapidly degrade turbine components.
Expertise within the industry suggests investing in multi-layered filters that balance efficiency and airflow dynamics. These advanced filters use nanofiber technology to enhance particle capture efficiency without compromising airflow, ensuring the turbine runs at peak performance. In trials, such technology demonstrated a 30% increase in turbine uptime and fuel efficiency.
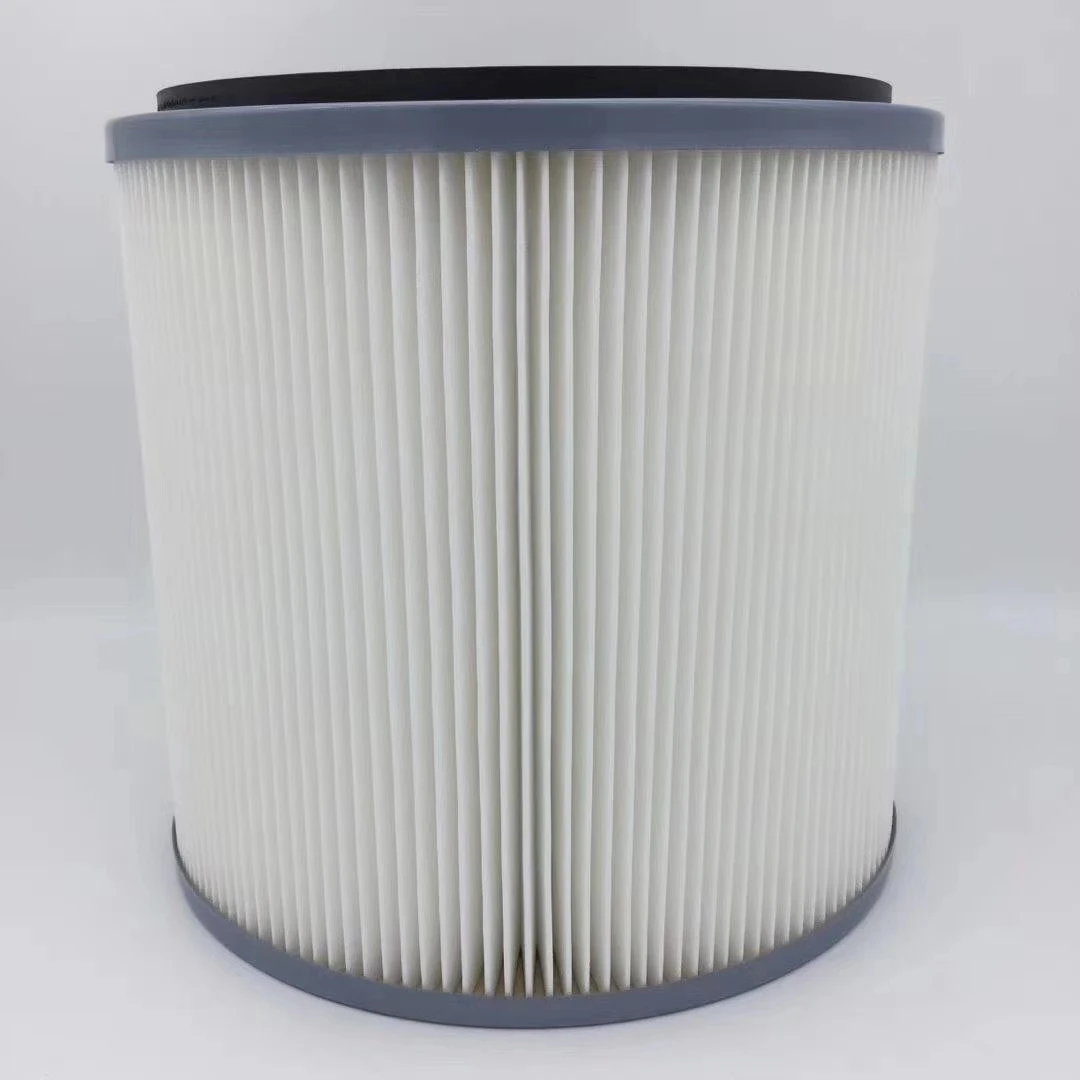
Authoritativeness in air filtration often comes from understanding the intricate balance between pressure drop and filtration effectiveness. The ASME has set stringent standards on these variables to guide industries in maximizing turbine lifespan and output. Following these standards can result in a 10% boost in operational efficiency, as confirmed by third-party studies.
Trustworthiness in filter selection is built on rigorous testing and certification. ISO 16890 is a benchmark for filter performance, focusing on real-world applications by testing filters against particles of all sizes. Filters that meet or exceed this standard are often heralded for their reliability and performance.
gas turbine air filter
The economic impact of selecting the correct air filter is expansive. The lifecycle cost analysis emphasizes that initial investment in superior filters yields significant savings by reducing the frequency of shutdowns and repairs. This forward-thinking strategy can lead to a marked increase in return on investment over the turbine's operational life.
From a sustainability perspective, high-efficiency air filters contribute to lower emissions by ensuring complete combustion. This not only complies with environmental regulations but also reduces the carbon footprint of industrial operations, aligning with global sustainability goals.
Case studies further underline the importance of the right air filter. One notable example is a power plant in Texas, which upgraded its filtration system and saw its operational efficiency soar by 15%, with a simultaneous drop in maintenance costs. These improvements were attributed to the advanced filter's ability to maintain cleaner turbine blades and reduce erosion.
In conclusion, the selection of a gas turbine air filter is a nuanced decision that demands an understanding of both technical specifications and operational impacts. By prioritizing advanced, certified filters, companies can achieve operational excellence, reduce costs, and meet regulatory demands efficiently. The investment pays off not just in immediate economic terms but also in ensuring sustainable and reliable energy production for the future.