The demand for antistatic filter elements has been escalating, particularly in industries where maintaining a static-free environment is crucial. These small yet indispensable components play a pivotal role in ensuring the safety and efficiency of operations in various sectors, from manufacturing to healthcare. Understanding the nuances of antistatic filter elements can make all the difference in optimizing the performance of your equipment and safeguarding your processes.
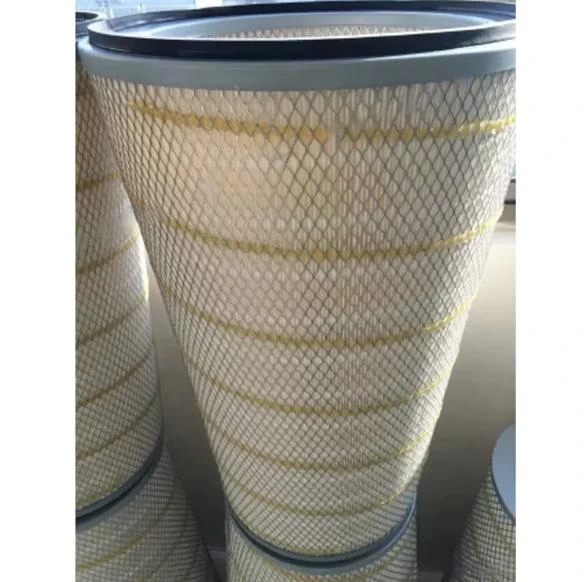
Antistatic filter elements are designed to prevent the accumulation of static electricity, which can cause catastrophic failures or inefficiencies in sensitive equipment. In industrial settings, where dusty or explosive atmospheres might be present, the build-up of static can lead to sparks, causing fires or explosions. Antistatic properties in filters ensure that any static charge is dissipated safely,
reducing the risk associated with such volatile environments.
The selection of the right antistatic filter element is critical, as it directly influences the system’s performance and longevity. Various materials are employed in the manufacture of these filters, including conductive carbon fibers, treated with antistatic coatings, or stainless steel mesh designed for harsh environments. Each material offers unique benefits and challenges, and choosing the right one depends on the specific requirements of your industry and application.

Beyond material considerations, the design of antistatic filter elements is central to their success in a given application. Some industries require filters with high airflow efficiency without sacrificing the filtration capabilities necessary to remove contaminants from the air. Balancing these factors demands an advanced understanding of filter dynamics and often involves collaboration with manufacturers who can customize filter elements to meet bespoke industrial needs.
In industries like pharmaceuticals, the presence of accurate antistatic filter elements can regulate cleanroom environments by controlling particle levels and preventing contamination. Similarly, in the semiconductor industry, where components are especially susceptible to electrostatic discharge (ESD), deploying antistatic solutions not only enhances the yield but also extends the lifespan of sensitive electronic equipment.
antistatic filter element
Alternatively, when it comes to environments handling chemicals or flammable substances, antistatic filters protect both the workforce and the product integrity by reducing the explosion risk due to static charges. This reduction in risk is further augmented by regulatory compliance—many industries are governed by stringent standards requiring the implementation of antistatic measures to ensure workplace safety.
The authoritative nature of incorporating antistatic filters is underscored by widespread industry recommendations and regulations, such as those from the Occupational Safety and Health Administration (OSHA) and the National Fire Protection Association (NFPA). Compliance with such standards not only enhances safety and operational efficiency but also mitigates legal risks.
Integrating antistatic filter elements effectively requires expertise not just in product selection, but also in understanding the installation environment and maintenance needs. Routine inspection and replacement of filters are necessary to maintain their antistatic properties and ensure ongoing protection. Manufacturers often offer detailed guidance and ongoing support to help businesses maximize the efficacy of these components throughout their lifecycle.
For companies investing in antistatic filter elements, reliability and trustworthiness in suppliers are paramount. Collaborating with reputable suppliers who have a proven track record of providing high-quality, certified filters can safeguard your investment and uphold your commitment to safety standards. Ensuring that your supplier possesses industry-specific expertise and offers postsale support can also play a critical role in optimizing the implementation and use of these filter elements.
In conclusion, incorporating antistatic filter elements into your equipment setup is not merely a precaution; it is an essential practice for enhancing operational efficiency, ensuring safety, and maintaining compliance with industry standards. As industries continue to evolve, the importance of antistatic filters will likely increase, underscoring the need for expertise and authoritative quality in the products selected. Whether for protecting sensitive electronics from ESD or minimizing explosion risks in volatile environments, the strategic implementation of antistatic filter elements stands as a testament to a company’s commitment to safety and performance excellence.