The efficiency and longevity of an industrial dust collection system often hinge on the choice of the right cartridge dust collector filter. Navigating through options can be overwhelming for any facility manager, especially with constant technological advancements and a myriad of choices. Yet, selecting the right cartridge filter is crucial for optimizing operational efficiency, enhancing air quality, and ensuring workplace safety.
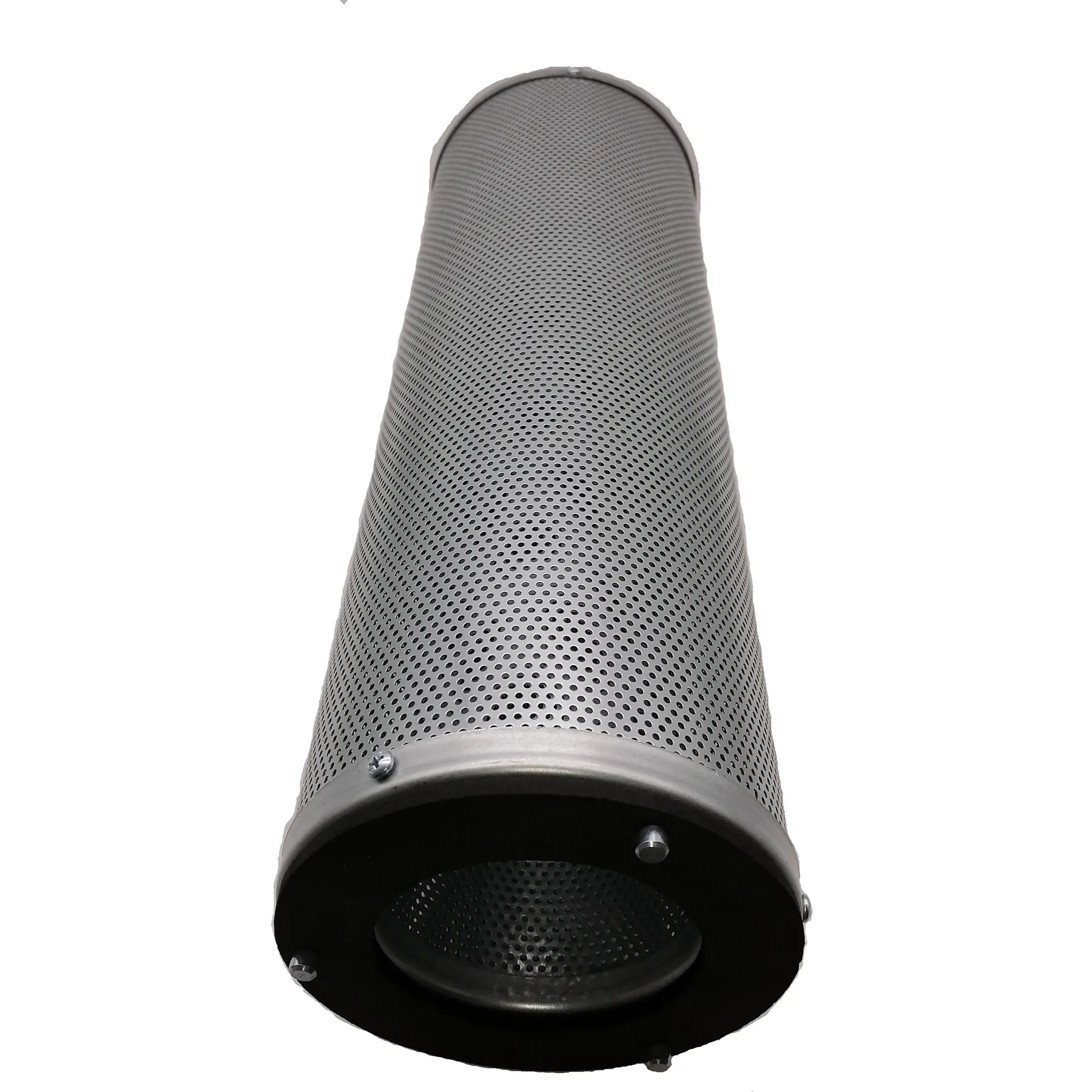
Cartridge dust collector filters play a pivotal role in capturing airborne dust and particulates that can potentially harm equipment and personnel. They are renowned for their exceptional filter surface area within a compact design, made possible through vertically set pleated media. This design maximizes the airflow path, effectively capturing dust and debris with greater ease compared to traditional baghouse filters. Furthermore, the innovative pleated construction reduces the frequency of change-outs and lowers maintenance expenses.
From a practical standpoint, selecting the appropriate cartridge filter involves consideration of the specific dust type, the operating environment, and regulatory compliance. An experienced facility manager will focus on filter media types such as cellulose, polyester, or a blend, selected based on dust characteristics. Cellulose is often preferred for cost efficiency in non-abrasive applications, while polyester media is lauded for its versatility and moisture resistance, instrumental in handling slightly sticky or hygroscopic dust types.
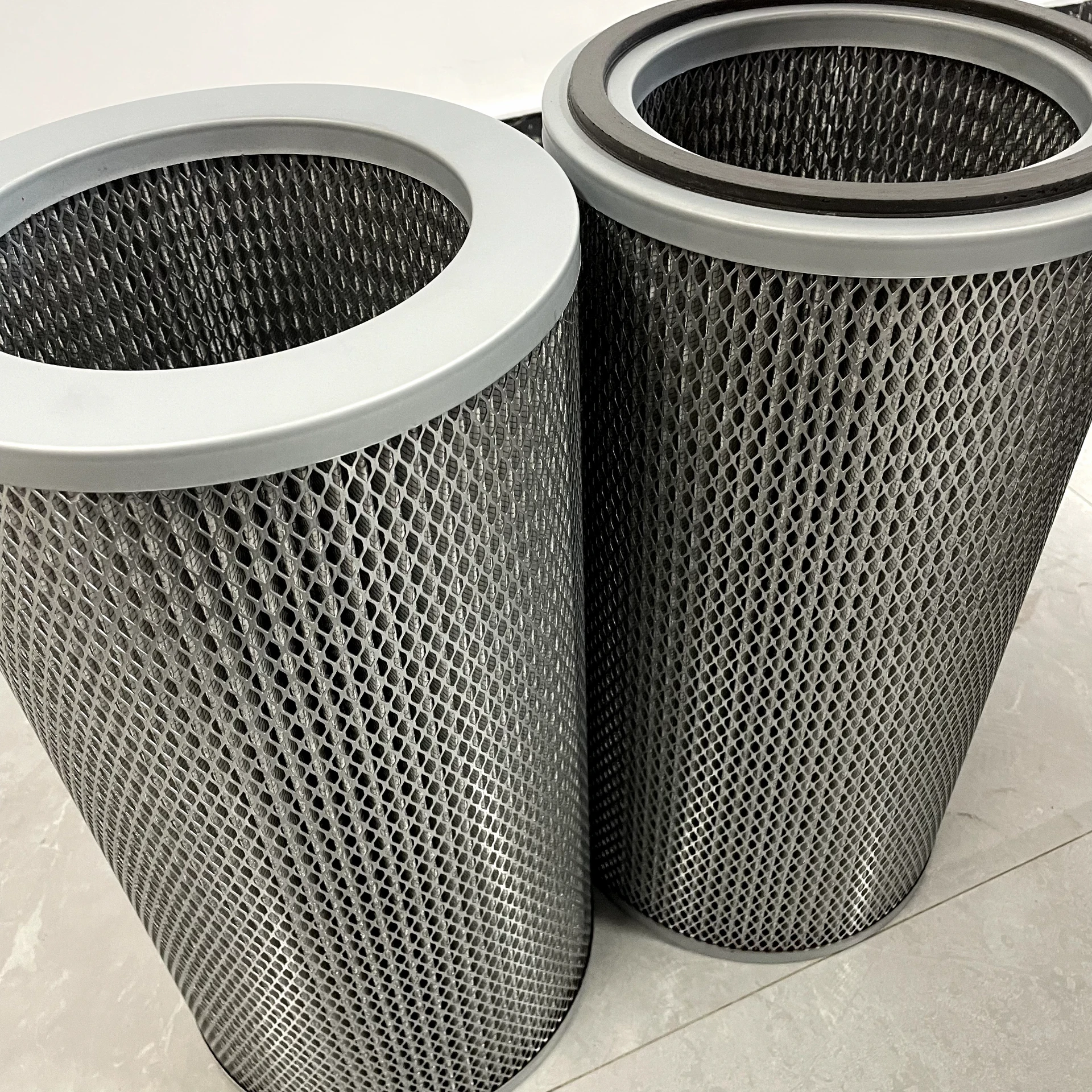
In terms of expertise, understanding the Minimum Efficiency Reporting Value (MERV) rating of a cartridge filter is paramount. Higher MERV ratings indicate finer filtration capability, which is crucial for operations where air purity and containment of sub-micron particles are critical. Dust particles from pharmaceutical manufacturing or chemical processes, for example, demand high MERV rated filters to ensure compliance with stringent health and safety standards.
cartridge dust collector filter
Authoritativeness in cartridge dust collector filter selection is also demonstrated through the knowledge of pulse-jet cleaning mechanisms. This system cleans the filters by blasting pulses of air to dislodge collected dust into a containment system. To optimize this feature, decision-makers must ensure compatibility with the operation's air pressure capabilities and the filter's designed cleaning frequency. Wrong settings can lead to premature filter wear or inefficient dust removal.
Building trustworthiness with stakeholders hinges on consistent performance and adherence to best practices in environmental safety. Employing cartridge filters that align with OSHA (Occupational Safety and Health Administration) guidelines and using HEPA (High-Efficiency Particulate Air) filters where necessary can cement an operation’s commitment to air quality and workforce welfare. Endorsements from industry participants and case studies highlighting cost savings and improved air quality bolster credibility, positioning the facility as a leader in safety and operational efficiency.
In conclusion, the strategic choice of a cartridge dust collector filter integrates experience with technical prowess, underscoring the need for thorough research and understanding of the dust collection landscape. By prioritizing the right mix of media, understanding regulatory requirements, and leveraging expert knowledge in filter maintenance and efficiency, facilities not only meet operational demands but also demonstrate a proactive approach to industrial hygiene and environmental stewardship. This approach fortifies the facility’s reputation as an enterprise that values innovation, safety, and sustainability in equal measure.