Ensuring optimal performance of gas turbines is a multifaceted challenge, one that pivots critically around the quality of air intake. The effectiveness of a gas turbine air intake filter is often a determining factor in the longevity and efficiency of these complex machines. As an expert with years of hands-on experience in the domain, the significance of a robust filtration system cannot be overstated.
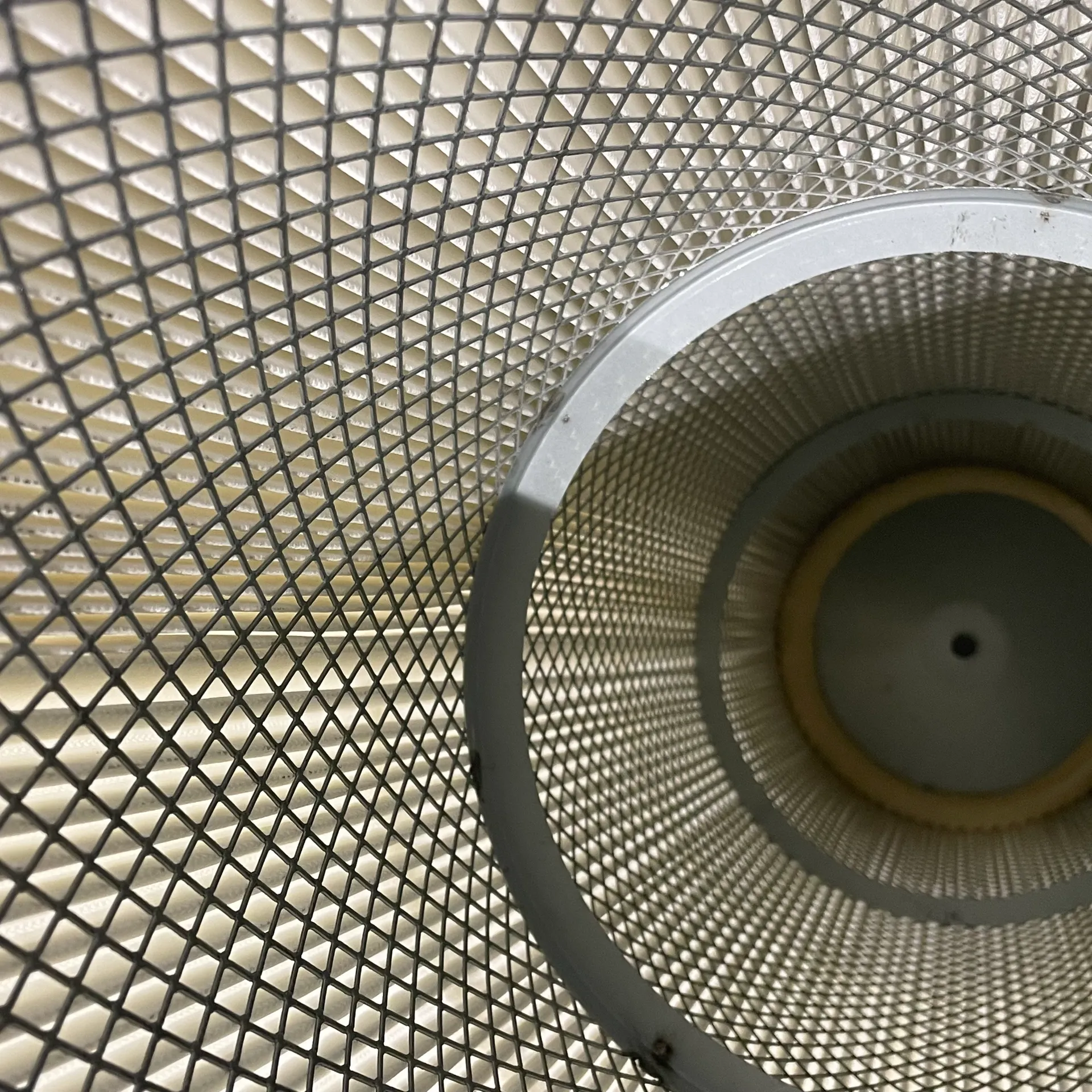
Gas turbines are powerhouses in various industries, driving multiple operations by converting chemical energy into mechanical energy. For these machines to function at their peak,
clean air intake is paramount. Contaminants such as dust, pollen, and other particulates can severely decrease the performance of gas turbines by causing erosion, corrosion, and fouling of turbine blades. This not only reduces efficiency but can also lead to costly maintenance and unexpected downtime.
From an expert perspective, a high-quality gas turbine air intake filter serves as the first line of defense in safeguarding turbine integrity. These filters are designed with advanced materials to capture a wide spectrum of particles, ensuring that only clean air reaches the turbine. The engineering behind these filters is nothing short of precise, often involving multi-layered media that maximizes dust-holding capacity while minimizing pressure drop.
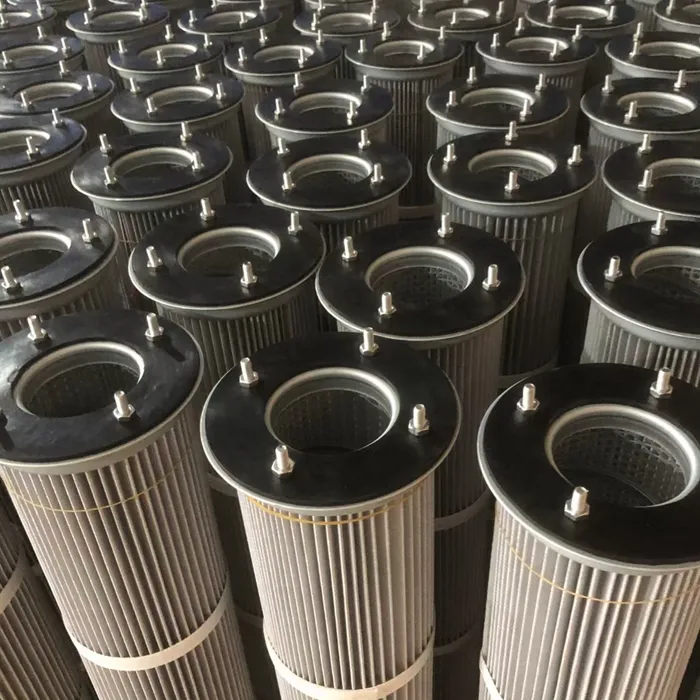
The choice of a gas turbine air intake filter should be informed by the specific environmental conditions surrounding the turbine's operation. For instance, turbines operating in desert environments require filters with enhanced dust-holding capabilities. On the other hand, turbines in coastal regions must tackle salt-laden air, necessitating filters that can prevent salt ingress. The adaptation to these conditions illustrates the expertise required in selecting the appropriate filter, emphasizing a site-specific approach rather than a one-size-fits-all solution.
gas turbine air intake filter
Authoritativeness in this field involves ongoing research and collaboration with industry leaders to innovate filtration technologies. The evolution of filtration materials, such as synthetic fibers and nanofibers, has marked a significant advancement in the efficiency and longevity of air intake filters. By staying at the forefront of these developments, professionals in the field offer trusted guidance and solutions, acknowledged through certifications and compliance with international standards.
Trustworthiness is cultivated through a commitment to quality and performance testing. Before an air intake filter is deemed suitable for use, it undergoes rigorous testing to ensure it meets stringent performance criteria under various operational stresses. Such dedication to reliability fosters a sense of security among users, knowing that their gas turbines are protected by a filtration system that has been thoroughly vetted.
Furthermore, real-world experiences speak volumes about the capabilities of gas turbine air intake filters. Take, for example, a coastal power plant experiencing reduced efficiency due to salt contamination. By upgrading to a filter specifically designed to counteract marine air issues, the plant not only improved its output but also extended the operational life of its turbines. These case studies provide tangible evidence of the benefits that can be achieved through the correct application of advanced filtration technologies.
In conclusion, the selection and implementation of a gas turbine air intake filter is a critical process that demands expertise and authority. By utilizing a filter system designed to meet the specific needs of its environment, operators ensure optimal performance and longevity of their turbines. Trust in these systems stems from their proven reliability and the commitment of industry experts to continual improvement and adaptation in the face of evolving challenges.