Navigating the complexities of optimizing turbine performance is becoming increasingly crucial in today's industries, where efficiency and ecological considerations are paramount. One pivotal aspect often overlooked, yet indispensable, involves the integration of air filter turbine systems. These components play a critical role in safeguarding turbine performance, extending equipment life, and optimizing energy output. Selecting the right air filter turbine system can significantly impact operational efficiency and cost-effectiveness.
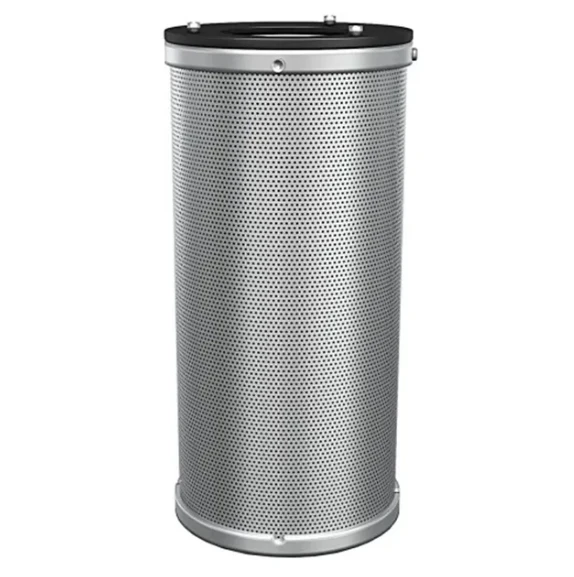
Air filter turbine systems operate as the guardians of turbines, filtering impurities from the air that enters these powerful machines. This role is essential because contaminants such as dust, pollen, and industrial pollutants can compromise the functionality and longevity of turbine components. Effective filtration ensures that only clean air interacts with the turbine, reducing wear and tear and minimizing maintenance requirements. Such preventative measures translate to a substantial reduction in operating costs and downtime, enhancing overall productivity and energy yield.
One of the vital factors when choosing an air filter turbine system is understanding the specific environmental conditions in which the turbine operates. Turbines situated in arid, dusty locales demand a filtration system capable of handling fine particulate matter. Conversely, turbines in regions with high humidity or industrial pollution may require specialized filters designed to trap both particulate and gaseous contaminants. Failing to align the filter choice with environmental demands could lead to inadequate protection and eventual turbine failure.
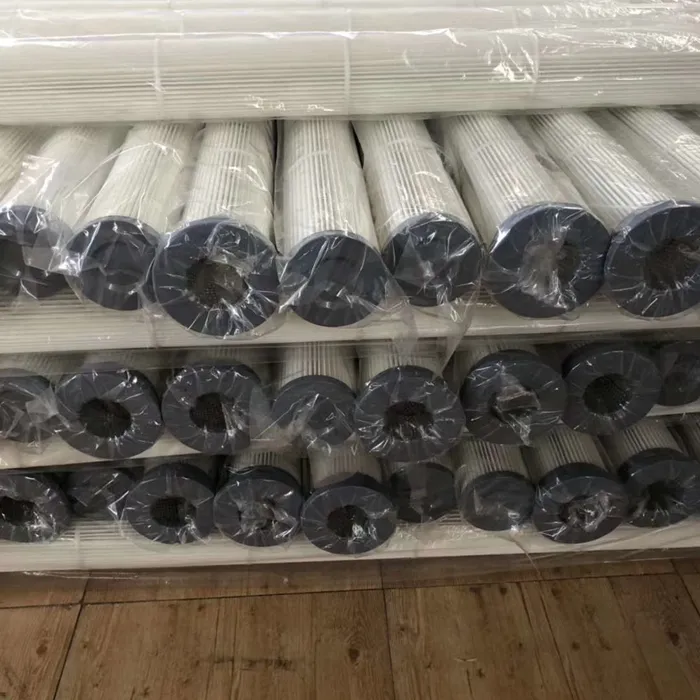
From a technical perspective, advancements in filter materials are reshaping the industry. The introduction of HEPA (High-Efficiency Particulate Air) and ULPA (Ultra Low Penetration Air) filters has revolutionized air filtration by providing superior filtration efficacy.
These filters can capture particles as small as 0.3 microns with high efficiency, making them ideal for environments with stringent air quality requirements. Additionally, the development of nanofiber technology represents a leap forward in filter design, offering enhanced durability and lower pressure drop across the filter media. Lower pressure drops are significant because they equate to less energy consumption during operation, thus aligning with energy-saving goals.
Beyond material innovations, the deployment of smart monitoring systems is driving air filter turbine advancements. These systems utilize sensors to continuously monitor the filter's condition, providing real-time data on filter performance and predicting when maintenance should occur. Such predictive maintenance tools are invaluable in preventing unexpected failures and optimizing the maintenance schedule, saving time and resources. This constant vigilance ensures that air filters are functioning optimally, further extending the life of turbines and improving their performance.
air filter turbine
The empirical evidence supporting the adoption of superior air filter turbine systems is robust. Studies indicate that implementing advanced filtration solutions can prolong turbine life by as much as 30%, significantly reducing maintenance costs and outage frequency. Companies that invest in these technologies report not only cost savings but also enhanced turbine reliability and efficiency. This correlation between high-quality filtration and operational excellence underscores the strategic importance of investing in advanced air filtration systems.
Industry experts resonate with the notion that future innovations will continue to evolve in the areas of filter material and design, aiming for even greater efficiency. What remains critical, however, is the bespoke nature of filter solutions tailored to specific turbine operations and environmental contexts. Businesses that recognize the strategic advantage of custom filter solutions will consistently outperform those using generic or outdated systems.
As the global economy continuously pushes towards sustainability, the role of air filter turbine systems gains even more prominence. Enabling cleaner energy production via efficient turbine operations not only meets regulatory demands but also aligns with corporate sustainability objectives. This alignment further enhances brand reputation and fortifies market position, offering a competitive edge in an increasingly eco-conscious world.
In conclusion, selecting the appropriate air filter turbine system is an investment with far-reaching implications for turbine performance and longevity. Companies must look beyond initial costs to consider the broader benefits of enhanced efficiency, reduced maintenance, and environmental compliance. Bolstered by technological advancements, air filter turbine systems will undoubtedly play an essential role in shaping the future of energy production, providing a cleaner and more efficient pathway forward.