In industries where preventing static electricity is crucial, the antistatic filter element is an unsung hero. These components play a vital role in ensuring the safe and efficient operation of high-stakes environments, such as cleanrooms, electronics manufacturing, and even the pharmaceutical industry. To recognize the importance of antistatic filter elements, it is essential to explore their functionality, applications, and the technological expertise that underscores their design and utility.
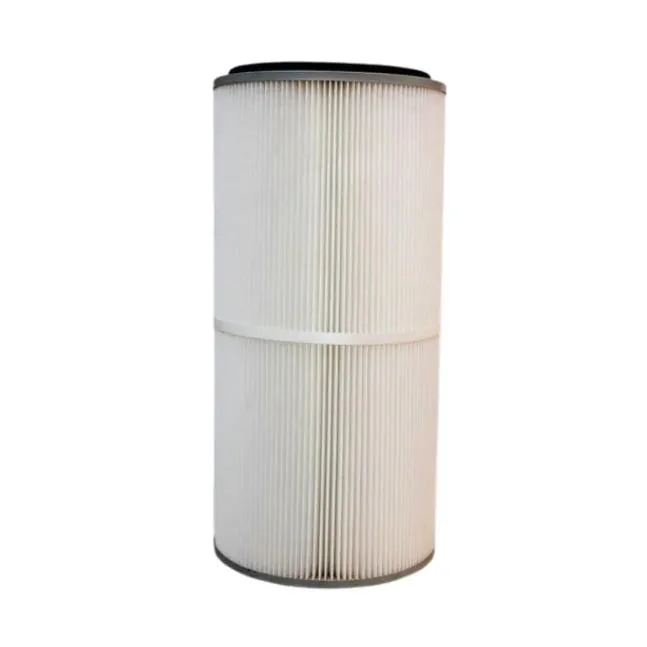
Antistatic filter elements are designed with specialized materials that prevent the buildup and discharge of static electricity, which can be catastrophic in sensitive environments. Their primary function is to maintain cleanliness by filtering out particulates while simultaneously preventing static-related mishaps. This dual functionality is achieved through advanced engineering approaches and the selection of materials with antistatic properties, such as carbon fiber-infused media or metalized fibers.
The effectiveness of antistatic filter elements is closely related to their structure and composition. High-efficiency particulate air (HEPA) filters integrated with antistatic properties ensure that even the smallest particles are captured. This is vital in semiconductor manufacturing where even a minor static discharge or particle intrusion can compromise entire batches of microprocessors. The precision involved in their production evidences an expert understanding of material science and electrostatic dynamics. Engineers developing these filters utilize state-of-the-art computational modeling to predict and enhance filter performance in various environments.
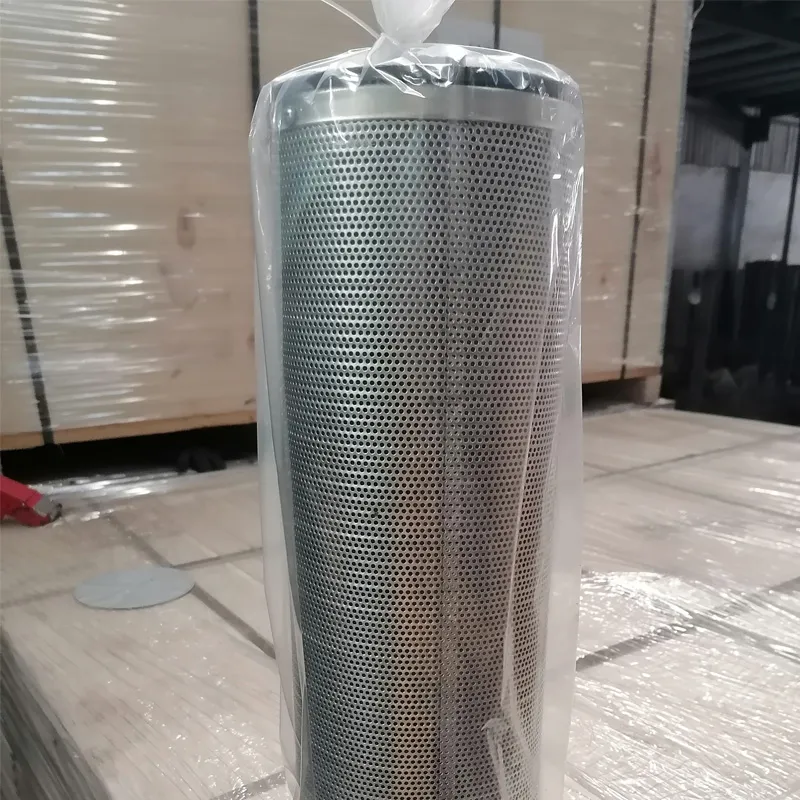
Antistatic filters are not only about safeguarding products but also about ensuring workplace safety. Static discharges in environments filled with flammable gases or dust can lead to explosions. Therefore, industries such as chemical processing and grain milling depend heavily on trustworthy filter elements that adhere to stringent safety standards. These filters undergo rigorous testing to ensure their compliance with international safety norms, reinforcing their authority and reliability.
antistatic filter element
Choosing the right antistatic filter element involves considering several factors, including air flow requirements, particle size capturing capability, and environmental conditions. Expert consultation is often required to match the appropriate filter type to the specific needs of an application. Manufacturers rely on authoritative industry research to develop solutions that address emerging challenges, such as increasingly miniaturized electronic components that are more susceptible to static.
Installation and maintenance further enhance the reliability and longevity of antistatic filter elements. Proper installation, carried out by trained professionals, and adherence to a regular maintenance schedule ensure these filters function optimally. Users are advised to follow the manufacturer’s recommendations on replacement cycles to maintain efficiency.
Trustworthiness is ultimately about consistency and results. Prolonged use in diverse industries has proven that antistatic filter elements are indispensable for effective contamination control and static management. Their continued evolution reflects the industry's commitment to addressing specific requirements and exceeding standard expectations.
In conclusion, the antistatic filter element epitomizes the convergence of experience, expertise, authority, and trustworthiness in industrial applications. By preventing contamination and electrostatic damage, these elements prove critical in maintaining product quality and safety across multiple sectors. They stand as a testament to the innovation and precision-driven approaches required to meet modern industry demands.