The innovation within the energy sector has significantly transformed the efficiency and reliability of gas turbines. At the heart of these advances, one cannot overlook the pivotal role played by gas turbine inlet filters. These components, acting as guardians of your turbine system, ensure optimal performance, longevity, and sustainability. To truly appreciate their importance, we must delve into the intricacies of their design and the palpable benefits they offer across various operational landscapes.
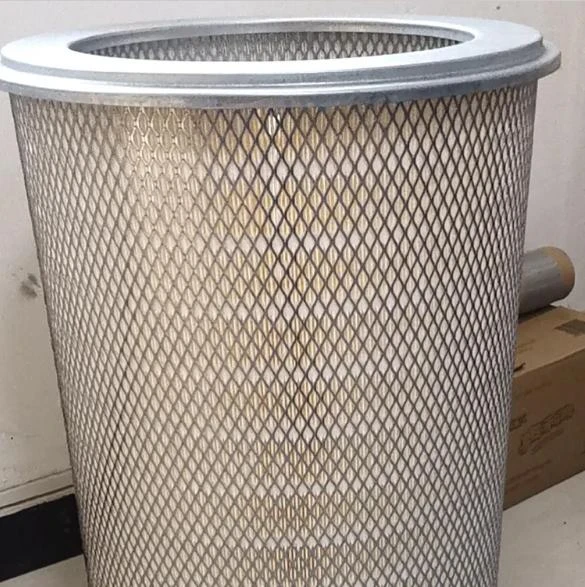
Gas turbine inlet filters are marvels of engineering, designed to tackle myriad environmental challenges that turbines face. This includes airborne contaminants such as dust, pollen, sea salt, and industrial pollutants, all of which can critically impair turbine efficiency. Not only do these filters prevent potential erosion and fouling of turbine blades, but they also optimize airflow, ensuring consistent operation at peak performance.
One striking real-world application can be seen in coastal power plants, where salt-laden air poses a significant threat. Here, enhanced filtration systems integrate specialized media that are resistant to salt penetration while maintaining excellent airflow. The results from several installations globally speak volumes—markedly reduced maintenance costs, diminished corrosion-related downtimes, and measurable improvements in output efficiency.
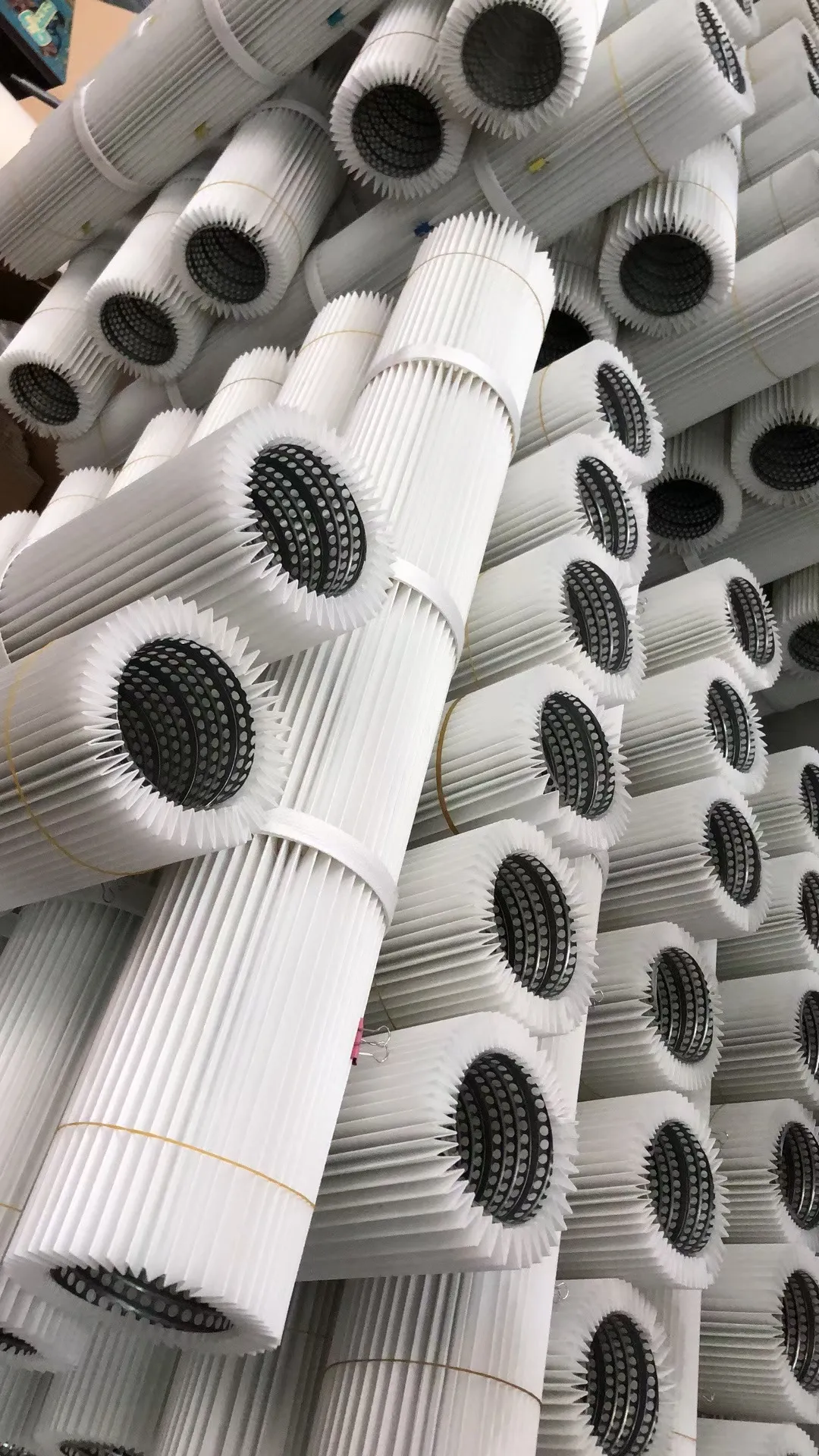
The professional craftsmanship behind these filters is grounded in fluid dynamics and material science. Leading manufacturers employ multilayered filtration technologies, combining pre-filters, high-efficiency particulate air (HEPA) filters, and coalescing filters. Each layer serves a unique function— from removing larger particulate matter to capturing fine aerosols and moisture. Expertise in selecting appropriate filtration media is crucial, as it impacts not only the filtration efficiency but also the pressure drop across the system, directly affecting turbine performance.
An authoritative industry perspective recognizes that inlet filters are not a one-size-fits-all solution. The specificity of environmental conditions necessitates a tailored approach. For instance, turbines operating in arid regions benefit from filters optimized for fines and low humidity, whereas those in high-moisture areas require robust water-resistance capabilities. Such customization demands consultation with authoritative figures in turbine technology—engineers who understand the delicate balance between environmental challenge and mechanical endurance.
gas turbine inlet filter
Trust in these systems is reinforced by rigorous testing and compliance with international standards such as ISO 29461. Manufacturers invest in state-of-the-art test facilities to simulate diverse operational environments, scrutinizing the performance and durability of their products over extended periods. Endorsements from industry bodies further instill confidence, as they validate the reliability and safety of these systems within operational settings.
For potential clients and industry stakeholders, implementing high-quality inlet filters translates into tangible benefits prolonged turbine lifespan, reduced operational hiccups, and substantial energy cost savings. Several case studies highlight the dramatic improvements seen in both performance metrics and environmental compliance standards post-installation. This creates an irrefutable case for incorporating advanced filtration solutions into existing turbine infrastructure.
Moreover, as sustainability continues to dominate global energy discourse, gas turbine inlet filters contribute significantly to this agenda. By ensuring turbines operate efficiently, they reduce unnecessary fuel consumption and consequent emissions, aligning operational goals with environmental stewardship. Advanced filters enable the seamless integration of gas turbines into greener mixed-energy grids, supporting a transitional approach to net-zero energy targets.
In conclusion, the indispensable role of gas turbine inlet filters emerges not only from a technical standpoint but also through their economic and environmental impact. Evolving from mere protective components to sophisticated enablers of efficiency and reliability, these filters represent a critical investment into the future of energy production. By harnessing the expertise of top engineers and maintaining unwavering dedication to quality, stakeholders can confidently navigate the demands of modern energy landscapes, assured of their operational resilience and competitive edge in a rapidly transforming market.