The efficiency and reliability of gas turbine systems significantly depend on the quality of air filtration. A well-designed gas turbine air filter does not only safeguard the turbine from harmful particulates but also ensures optimal operation and longevity. Here are the key considerations and advanced insights for leveraging gas turbine air filters in enhancing turbine performance
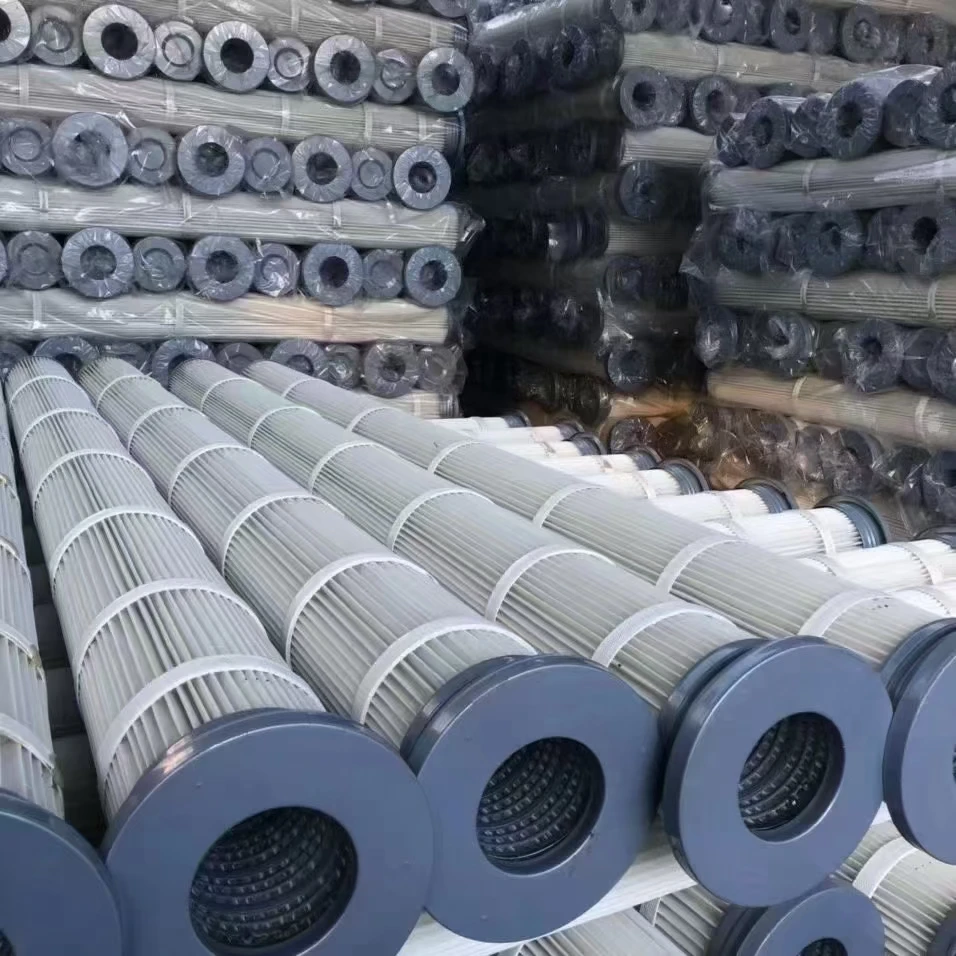
Gas turbines, being the powerhouses of many industrial operations, require a sophisticated filtration system capable of withstanding harsh environmental conditions. A high-quality air filter is crucial as it prevents foreign particles like dust, dirt, pollen, and other contaminants from entering the turbine system. When these impurities infiltrate the turbine, they can cause abrasion, erosion, and corrosion that lead to reduced efficiency and increased maintenance costs.
The modern gas turbine air filter is designed with multi-layered filtration media and precise engineering. State-of-the-art filtration systems typically incorporate materials such as high-efficiency synthetic fibers or nanofibers. These materials are specifically chosen for their ability to capture fine particles, thus providing superior protection compared to traditional filters. These advanced filters are often coupled with hydrophobic coatings, which are instrumental in repelling water and any moisture-laden particulates that could potentially cause rust or damage to the internal components of the turbine.
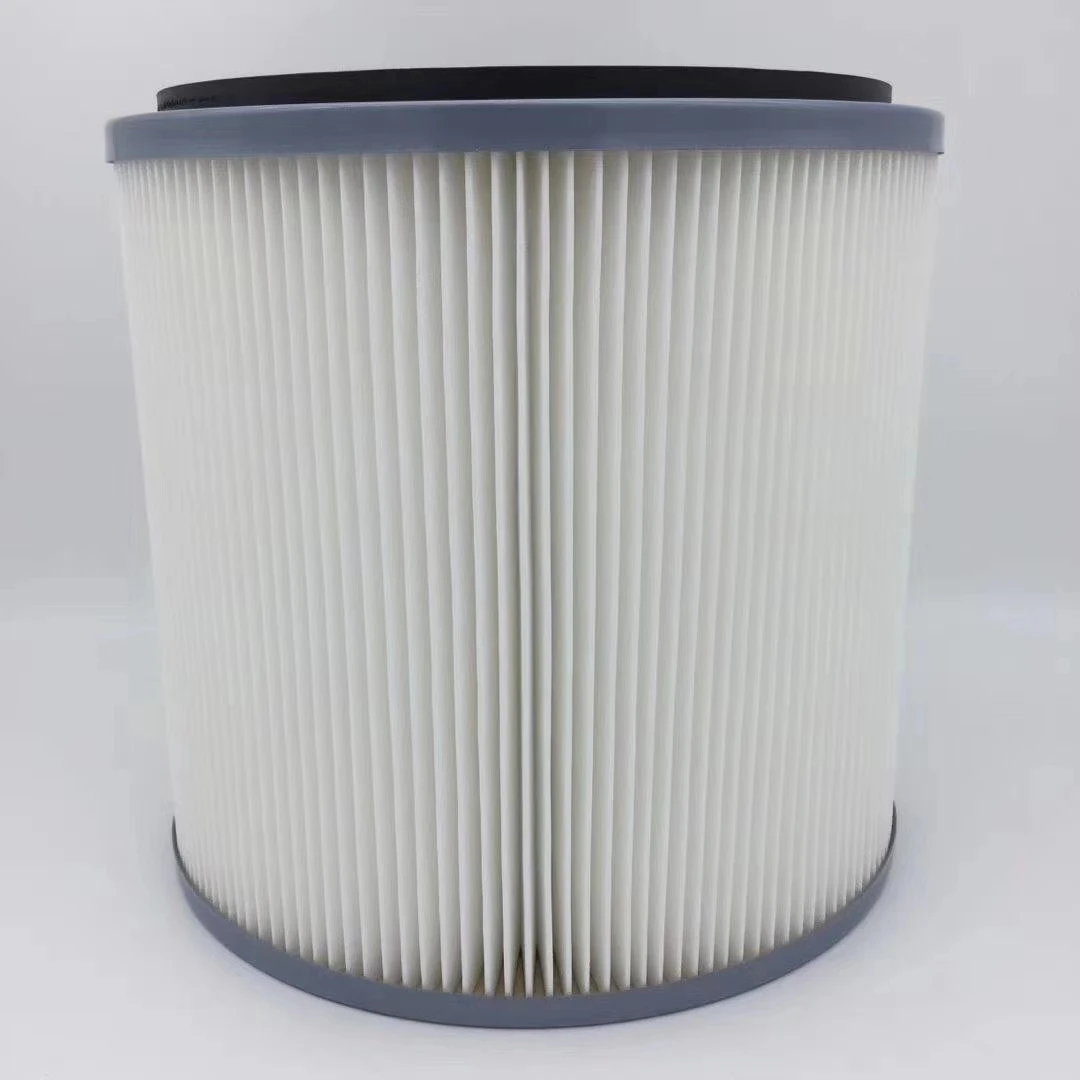
Moreover,
selecting the right type of air filter is pivotal. The choice largely depends on the specific environmental conditions in which a turbine operates. For example, turbines in arid, dusty regions require filters with a high dust holding capacity, while those in humid areas might need filters with enhanced moisture resistance. Efficiency ratings such as the Minimum Efficiency Reporting Value (MERV) or Efficiency Particulate Air (EPA) classifications provide further guidance in selecting the appropriate filter type.
gas turbine air filter
The installation process and maintenance practices also play crucial roles in the effectiveness of gas turbine air filters. Routine inspections and timely replacements are vital in maintaining the filter's performance. As an expert, it is advisable to establish a maintenance schedule that considers both manufacturer recommendations and operational demands. Implementing advanced monitoring systems can preemptively detect blockages or performance degradation, thus allowing timely interventions before a problem exacerbates.
Leveraging data analytics and predictive maintenance technologies can substantially minimize operational disruptions. IoT-enabled filtration systems offer real-time data that can be analyzed to predict potential failures and optimize filter replacement intervals. This approach not only enhances turbine reliability but also solidifies trust in the operational integrity of the entire system.
In conclusion, the importance of a meticulously chosen and maintained gas turbine air filter cannot be overstated. Integrating cutting-edge technologies with expert knowledge fosters an environment of reliability and performance—two attributes paramount for any industrial operation relying on gas turbines. By aligning maintenance practices with technological advancements, operators can ensure their turbine systems are not just protected but also harness their full operational potential, ultimately driving both efficiency and cost-effectiveness in energy production.