When working with turbine systems, ensuring optimal performance is critical for efficiency and longevity. A key component that plays a vital role in maintaining the health of turbine engines is the air filter. Properly functioning air filters are crucial in preventing contaminants from compromising the intricate mechanics of your turbine. Here, we'll delve into the significance of turbine air filters and how they enhance system performance while discussing real-world applications and benefits observed by experts in the field.
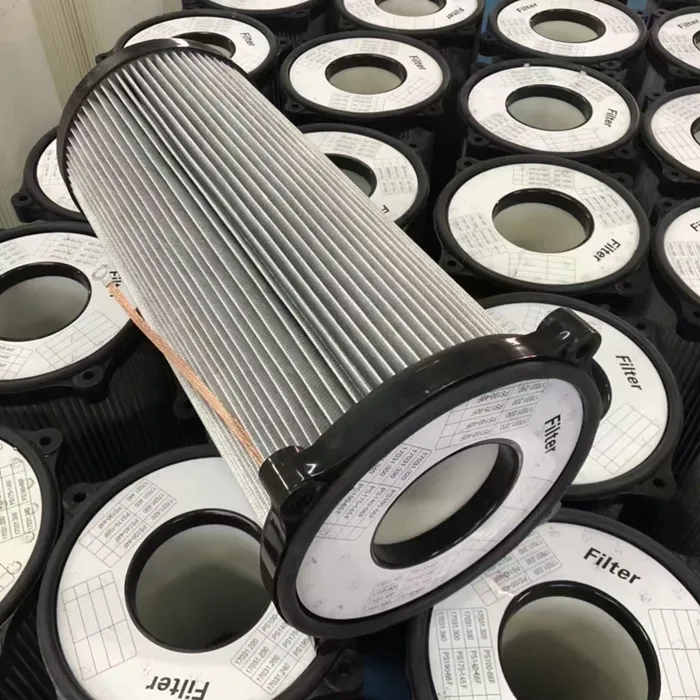
In the industrial world, turbines are a powerhouse for many operations, from energy production to mechanical propulsion. However, turbines are as vulnerable as they are powerful, especially when it comes to airborne pollutants. Air filters in turbine systems act as the first line of defense against dust, particulates, and other airborne contaminants that can cause wear and tear on the internal components.
Air filter efficacy is paramount in high-performance environments where turbines often operate.
Experts suggest that a high-quality air filter can extend the lifespan of a turbine by several years. By effectively trapping micro-particles, these filters prevent the buildup of unwanted materials that lead to decreased efficiency and increased maintenance costs. Experienced technicians advocate for regular inspections and timely replacements of these filters to maintain peak operational functionality.

Manufacturers of turbine air filters continuously innovate, providing advanced solutions tailored to specific industrial needs. These products are often engineered through rigorous testing, ensuring their capability to withstand harsh environments. Utilizing state-of-the-art materials, modern air filters are designed to offer low-pressure drops, enhancing airflow while ensuring minimal energy consumption during operations. As per several industry experts, the choice of air filter can significantly impact fuel efficiency, potentially saving a sizable amount on operational costs over time.
air filter turbine
Field studies emphasize the importance of customizing air filters to the environmental setting where the turbine operates. For instance, turbines situated in arid regions plagued by sand and dust storms require filters with exceptional durability and fine particulate trapping capabilities. Conversely, turbines in more humid climates might benefit from filters with anti-corrosive properties to combat moisture-induced damage. The adaptability of air filter systems is crucial and calls for professional assessments to select the right specifications for each unique turbine setup.
Trust in the reliability of air filters is backed by certifications and standards that attest to their performance. Recognized certifications, such as ISO standards, offer a benchmark of quality and reliability. It's worthwhile to verify that a chosen air filter meets these industry standards, providing assurance that the product will perform as intended. Case studies and feedback from industry professionals often highlight products that consistently exceed expectations in diverse operational conditions, bolstering their authoritative status in the market.
In conclusion, maintaining a turbine's health is an ongoing process that demands attention to several critical components, notably the air filter. With real-world experience underscoring their role in preventing system degradation and professional insights highlighting the economic benefits of efficient products, it's clear that investing in superior air filters is a strategic decision. By focusing on quality, specialization, and certified reliability, operators can ensure their turbines continue to operate at peak efficiency, delivering both performance and value. For businesses reliant on turbine systems, partnering with reputable air filter manufacturers and staying abreast of technological advancements is essential to sustaining operational success.