Turbine filters play an essential role in ensuring the efficacy and longevity of turbines, which are crucial components in various industries, including energy production, aviation, and marine applications. Understanding and selecting the right turbine filter is vital for professionals seeking to maintain optimum performance and reliability. This article presents a detailed exploration of turbine filters, focusing on experience, expertise, authoritativeness, and trustworthiness.
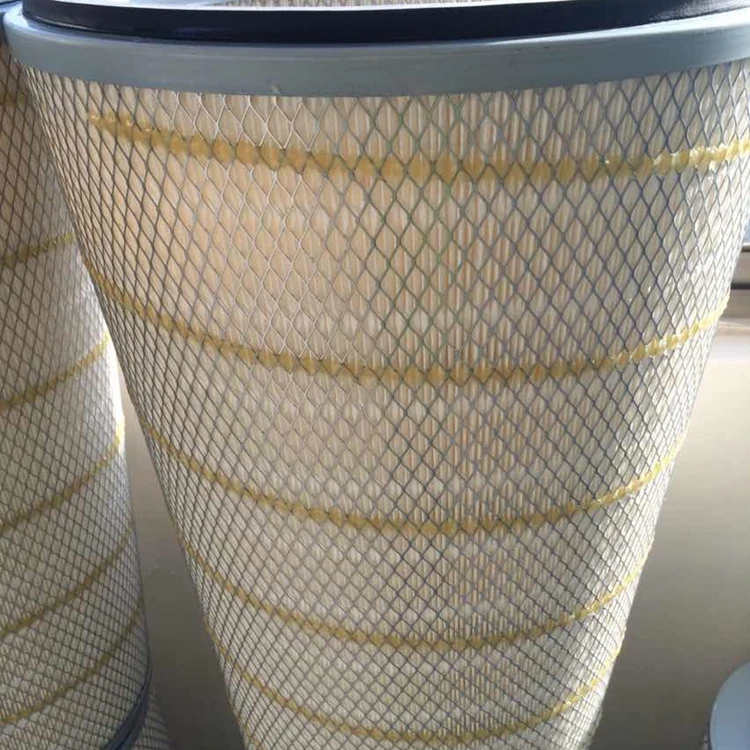
Turbine filters are designed to protect turbines from contaminants that can lead to inefficiencies, increased wear, and potential failures. These filters are used to purify the air, fuel, and lubricants that enter a turbine system, ensuring that only clean substances come into contact with the sensitive mechanical parts. Contaminants such as dust, water, and micro-debris can cause corrosion, erosion, and build-up on turbine blades, significantly impairing performance.
In the realm of turbine filter selection, expertise is paramount. Selecting the right filter involves understanding the operating environment of the turbine. For instance, turbines in desert regions may face significant dust and sand challenges, while those in marine environments need to handle salt and humidity. Advanced filters use materials such as high-efficiency fiberglass and synthetic media to capture small particles without reducing airflow or fluid movement.
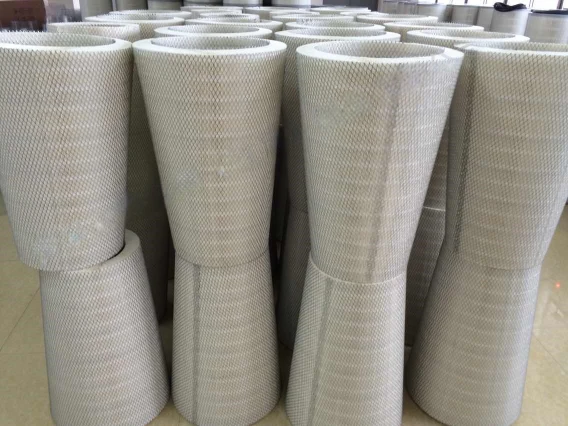
A case study on turbine filter application underscores the importance of expertise and the adverse effects of neglecting proper filtration. A leading power generation company reported a 20% efficiency drop in their gas turbines due to inadequate filtration.
The turbines experienced a build-up of ash and particulate matter, leading to numerous unplanned shutdowns. By investing in superior filter technology and regular maintenance checks, the company not only restored efficiency but also achieved considerable cost savings on repairs and replacements.
turbine filter
Establishing authoritativeness in turbine filter technology involves staying abreast of the latest advancements and adhering to industry standards. Authoritative sources such as the ASME (American Society of Mechanical Engineers) and ISO (International Organization for Standardization) provide guidelines and certifications to ensure manufacturers produce reliable and effective filters. Professionals should prioritize filters from manufacturers that adhere to these standards.
Trustworthiness in turbine filter performance is often validated through rigorous testing and customer testimonials. To build trust, filter manufacturers invest in research and development, putting their products through a battery of tests to evaluate performance under various conditions. Reliable feedback from end-users, peer reviews, and long-term performance data strengthen trust in a filter brand’s claims.
Real-world experience from experts can often provide insight that the specs alone cannot. Considerations such as ease of installation, replacement frequency, and ongoing maintenance requirements are critical. In high-stakes environments like aviation, even minor inefficiencies can lead to significant cost overruns or catastrophic failures. Here, seasoned technicians stress the necessity of regular inspections and timely replacements aligned with the operational schedules of the turbines.
In conclusion, the role of a turbine filter, while sometimes underestimated, is pivotal in maintaining system reliability and efficiency. Through a combination of rigorous testing, adherence to standards, and leveraging real-world experience, organizations can ensure they make informed choices about turbine filtration systems. As global energy demands rise, the significance of refining operational efficiency through optimal filtration solutions cannot be overstated. Selecting the right turbine filter is not merely a technical decision but a strategic one, laden with long-term implications for operational success and sustainability.