Selecting the right dust extractor cartridge filter is crucial for efficient air quality management in various industrial environments. These filters are designed to capture and contain fine particulate matter, ensuring a clean and safe workspace. Their effectiveness can often be the difference between compliance and costly downtime due to environmental health and safety violations.
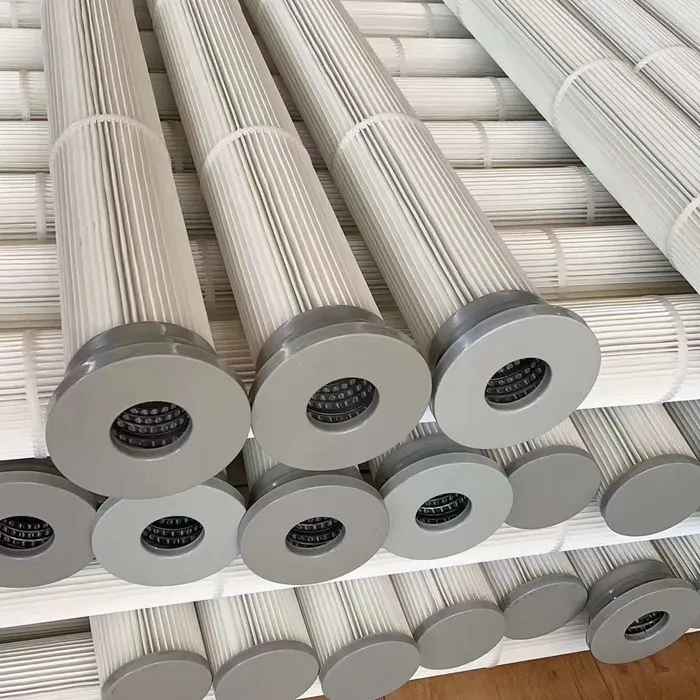
When evaluating dust extractor cartridge filters, it's important to understand the intricacies of their operation. Typically, these filters work within dust collection systems that utilize a fan-powered vacuum to draw in contaminated air. The air then passes through the cartridge filter, which traps dust and particles while allowing clean air to pass through.
One key component of these filters is the filter media. Polyester, cellulose, and nano-fibre are common materials used, each offering unique benefits. Polyester media, known for its durability and resistance to abrasion, is optimal for industrial environments with high particulate loads. In contrast, cellulose provides good filtration efficiency and cost-effectiveness but may not last as long in harsher settings. Nano-fibre media stand out for their high efficiency in capturing submicron particles, making them suitable for industries where fine dust is a concern, such as pharmaceuticals and electronics.
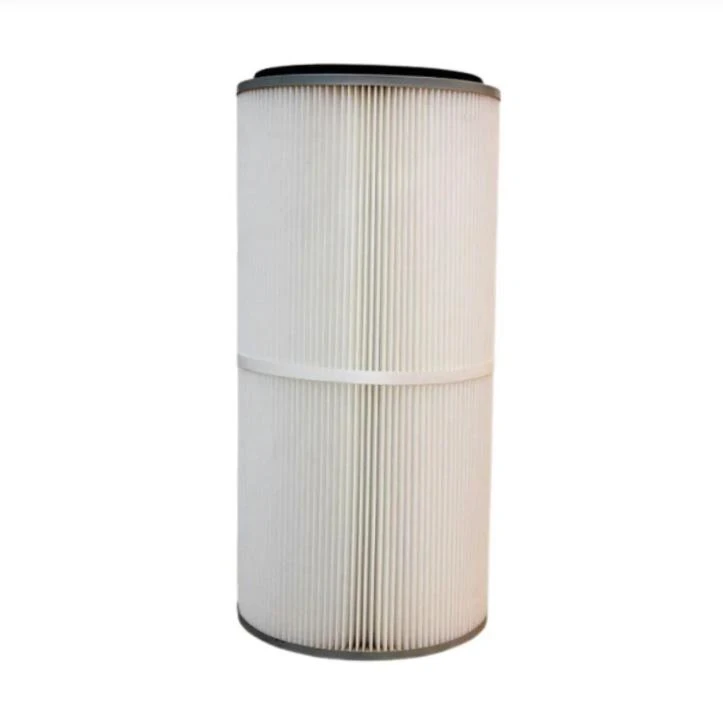
However,
identifying the right filter goes beyond just material selection. Compatibility with the dust collection system is essential. Choosing a filter that matches the airflow and pressure drop specifications of the system ensures maximum efficiency and longevity. Experts often recommend consulting with manufacturers or professional service providers to guarantee a precise fit and optimal performance.
Proper maintenance and replacement schedules also play a significant role in the effectiveness of dust extractor cartridge filters. Clogged filters can lead to reduced performance and increased energy costs, as the system must work harder to pull air through the obstructed media. A regular maintenance plan that includes inspection, cleaning, and timely replacement can enhance the lifespan of both the filters and the dust collection system.
dust extractor cartridge filter
In industries where dust collection is critical, such as woodworking, metalworking, and food processing, the impact of high-quality dust extractor cartridge filters can be profound. By improving air quality, they contribute to safer working conditions, reduce equipment wear and tear, and ensure compliance with occupational health regulations. This, in turn, builds trust with employees and clients, highlighting an organization’s commitment to workplace safety and sustainability.
Furthermore, advancements in filter technology continue to drive industry standards forward. Recent innovations, such as anti-static filters and those with integrated fire-retardant properties, are adding layers of safety in environments where combustible dust is a risk. Staying informed about these developments ensures that businesses can make educated decisions and adopt solutions that meet evolving safety standards.
Expert testimonials and case studies have long highlighted the advantages of investing in quality filter systems. Businesses sharing their experiences often report not only compliance but also significant cost savings related to energy use and system maintenance. Engaging with professional forums, industry conferences, and technical workshops can provide valuable insights and foster an environment of continuous learning and improvement.
Moreover, fostering a culture of education and awareness among employees regarding the operation and maintenance of dust extraction systems amplifies the efficacy of these devices. Training programs should focus on operational safety, the importance of scheduled maintenance, and recognizing signs of wear or failure in filter units.
In conclusion, the strategic selection, installation, and maintenance of dust extractor cartridge filters are integral to operational success in industrial settings. Recognizing the multifaceted impact of these systems—from enhancing workplace safety and compliance to driving cost-efficiency—highlights their indispensable role. Businesses that prioritize expert advice, invest in quality solutions, and foster informed workplace cultures will undoubtedly see the long-term benefits.